Iron casting, an ancient yet enduring art, stands as a testament to human ingenuity and the evolution of manufacturing processes. This technique, involving the pouring of molten iron into molds to create a vast array of shapes and components, has significantly contributed to the development of industries ranging from automotive to construction, machinery, and even art.
The Roots of Iron Casting
The origins of iron casting can be traced back to ancient civilizations like China, where early forms of cast iron were produced as early as the 5th century BC. However, it was during the Industrial Revolution that iron casting truly flourished, driven by advancements in technology and the rising demand for durable, mass-produced parts. Cast iron's unique properties—its high strength, durability, and ability to withstand extreme temperatures—made it a preferred material for everything from engine blocks and machine tools to architectural elements such as railings and decorative facades.
The Casting Process From Molten Metal to Finished Product
The process of iron casting begins with the preparation of a pattern, typically made of wood or metal, which replicates the final product's shape in exact detail. This pattern is then used to create a mold, usually from sand, into which the molten iron is poured. The sand mold, composed of two halves, allows for the easy removal of the casting once it has cooled and solidified.
Once the mold is ready, the actual casting takes place in a foundry. Molten iron, heated to temperatures exceeding 1400°C (2550°F), is carefully ladled from a furnace and poured into the mold's cavity. The cooling and solidification phase is critical, as it determines the casting's integrity and dimensional accuracy. After cooling, the sand mold is broken away, revealing the raw casting. This is followed by a series of finishing processes, including grinding, machining, and heat treatment, to achieve the desired surface finish and mechanical properties.
Varieties of Iron Castings
Cast iron is not a single entity but encompasses several types, each suited for specific applications based on their composition and properties
- **Grey Iron** Characterized by its graphite flakes that give it a distinctive gray color, grey iron is known for its good machinability, vibration damping, and excellent wear resistance. It is widely used in engine blocks, cylinder heads, and brake discs It is widely used in engine blocks, cylinder heads, and brake discs
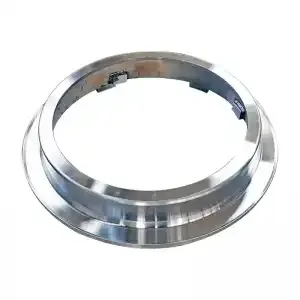
It is widely used in engine blocks, cylinder heads, and brake discs It is widely used in engine blocks, cylinder heads, and brake discs
iron casting.
- **Ductile Iron** Also called nodular or spheroidal graphite iron, ductile iron contains graphite in spherical form, providing improved toughness and ductility compared to grey iron. Its enhanced properties make it suitable for heavy machinery parts, pipe systems, and automotive suspension components.
- **White Iron** With a white, crystalline structure due to the presence of carbides, white iron is extremely hard and wear-resistant but brittle. It finds application in wear-resistant parts like mill liners and grinding balls.
- **Malleable Iron** Through a special heat treatment process, malleable iron acquires greater ductility than regular cast iron, making it easier to form and weld. It is often used in complex-shaped, high-stress applications such as pipe fittings and agricultural equipment.
Challenges and Innovations
Despite its longevity, the iron casting industry faces ongoing challenges related to energy consumption, environmental impact, and the quest for higher efficiency and precision. Modern foundries are adopting advanced technologies like computer-aided design (CAD), computer numerical control (CNC) machining, and 3D printing for pattern making, along with robotics for increased automation and consistency. Additionally, sustainable practices, including the recycling of sand and scrap iron, are being emphasized to reduce waste and ecological footprint.
In conclusion, iron casting remains a cornerstone of modern manufacturing, offering unparalleled versatility and durability across various sectors. As technology continues to advance, so too will the capabilities of this age-old practice, ensuring its relevance well into the future. By combining traditional techniques with innovative methodologies, the iron casting industry perpetuates a legacy of strength and adaptability, casting a lasting impact on our industrialized world.