Eutectic Aluminum Alloys Revolutionizing Lightweight Manufacturing
In the realm of materials science, eutectic aluminum alloys have emerged as a game-changer, particularly in industries where lightweight, high-strength, and superior thermal conductivity are paramount. These alloys, characterized by their unique eutectic composition, offer an exceptional blend of properties that conventional aluminum alloys often struggle to match. This article delves into the fundamentals of eutectic aluminum alloys, their manufacturing processes, and the extensive applications they facilitate across various sectors.
**Understanding Eutectics A Fundamental Perspective**
A eutectic alloy refers to a specific mixture of two or more components, which, when combined in precise proportions, exhibit the lowest possible melting point compared to any other combination of the same elements. In the context of aluminum alloys, this usually involves blending aluminum with other elements like silicon, copper, or magnesium to form a microstructure where each constituent solidifies simultaneously, creating an interlocking crystal structure. This unique arrangement imparts extraordinary mechanical and thermal characteristics to the material.
**Manufacturing Processes and Characteristics**
The production of eutectic aluminum alloys typically involves precise control over the alloying process, ensuring the correct balance of elements to achieve the desired eutectic composition. Techniques such as casting, powder metallurgy, and advanced manufacturing methods like additive manufacturing (3D printing) play crucial roles. One notable advantage of these alloys is their capacity for near-net-shape manufacturing, reducing waste and enhancing efficiency during production.
Key properties of eutectic aluminum alloys include
1. **Enhanced Strength-to-Weight Ratio** By incorporating elements like silicon, these alloys can achieve exceptional strength without significantly increasing weight, making them ideal for aerospace and automotive applications.
2. **Superior Thermal Conductivity** Eutectic aluminum alloys excel in heat dissipation, vital for high-performance electronics and heat exchangers.
3. **Improved Wear Resistance** The intermetallic phases in the eutectic structure contribute to increased hardness and wear resistance, suitable for tooling and machining components **Improved Wear Resistance** The intermetallic phases in the eutectic structure contribute to increased hardness and wear resistance, suitable for tooling and machining components
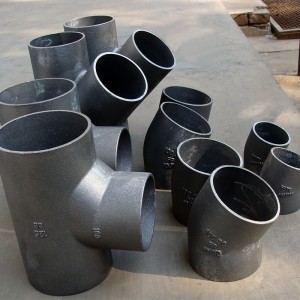
**Improved Wear Resistance** The intermetallic phases in the eutectic structure contribute to increased hardness and wear resistance, suitable for tooling and machining components **Improved Wear Resistance** The intermetallic phases in the eutectic structure contribute to increased hardness and wear resistance, suitable for tooling and machining components
eutectic aluminum alloy.
4. **Ease of Processability** Despite their advanced properties, eutectic aluminum alloys can be readily machined, welded, and formed, providing versatility in design and fabrication.
**Applications Spanning Diverse Industries**
The versatility of eutectic aluminum alloys has led to their widespread adoption across numerous industries
- **Aerospace** Lightweight yet robust, these alloys find application in aircraft structures, engine parts, and space vehicles, contributing to fuel efficiency and payload capacity enhancement.
- **Automotive** In the quest for lighter cars with improved fuel economy, eutectic aluminum alloys are used in engine blocks, suspension systems, and structural components.
- **Electronics** Their excellent thermal conductivity makes them suitable for heat sinks in high-power electronic devices, ensuring efficient cooling and longevity.
- **Tooling and Machinery** The enhanced wear resistance of certain eutectic alloys renders them ideal for dies, molds, and high-speed cutting tools.
- **Renewable Energy** From solar panel frames to wind turbine components, these alloys support the growth of sustainable energy technologies due to their durability and lightness.
**Challenges and Future Prospects**
While eutectic aluminum alloys present numerous advantages, challenges persist. Cost-effectiveness, especially compared to traditional aluminum alloys, and the complexity of achieving consistent eutectic structures at an industrial scale are among the key considerations. However, ongoing research and development efforts aim to address these issues through innovative processing techniques and the discovery of new alloy compositions.
The future of eutectic aluminum alloys looks promising, with advancements in material science and manufacturing technology poised to unlock even greater potential. As industries continue to seek lightweight, high-performance materials to meet the demands of sustainability and technological progress, eutectic aluminum alloys will undoubtedly remain at the forefront of innovation.