Lost Wax Casting A Timeless Technique for Producing Precision Parts
Lost wax casting is an ancient technique that has been used for centuries to create intricate and delicate metal parts. This method involves creating a wax model of the desired part, coating it with a refractory material, and then melting away the wax to leave a hollow mold. Molten metal is then poured into the mold, solidifying and taking the shape of the original wax model. Once the metal has cooled and hardened, the mold is broken apart to reveal the finished part.
One of the key advantages of lost wax casting is its ability to produce parts with complex geometries and fine details that would be difficult or impossible to achieve using other manufacturing methods. This makes it particularly well-suited for creating parts for industries such as jewelry, aviation, and automotive. Lost wax casting can also be used to produce parts in a wide range of materials, including gold, silver, platinum, and various types of alloys.
Another advantage of lost wax casting is its high level of precision and consistency. Because the wax model is used as the basis for the final part, variations in the size and shape of the original model are transferred to the final product Because the wax model is used as the basis for the final part, variations in the size and shape of the original model are transferred to the final product
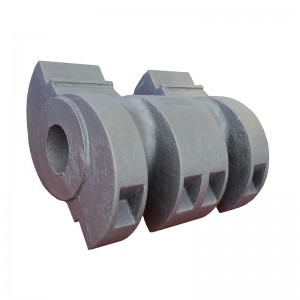
Because the wax model is used as the basis for the final part, variations in the size and shape of the original model are transferred to the final product Because the wax model is used as the basis for the final part, variations in the size and shape of the original model are transferred to the final product
lost wax casting parts manufacturers. This means that lost wax casting can be used to produce parts with extremely tight tolerances, making it an excellent choice for applications where accuracy is critical.
Lost wax casting is also a highly versatile process that can be adapted to produce a wide variety of different parts. For example, the size and shape of the mold can be adjusted to produce parts of different sizes and shapes, and the type of refractory material used can be varied to produce parts with different properties. This flexibility makes lost wax casting an attractive option for manufacturers who need to produce a diverse range of parts.
In conclusion, lost wax casting is a timeless technique that continues to be widely used in industries around the world. Its ability to produce complex and precise parts, combined with its versatility and high level of precision, make it an invaluable tool for manufacturers seeking to create high-quality metal components.