In the realm of industrial applications, the concept of the material heat exchanger has emerged as a critical component, influencing energy efficiency and operational productivity. At its core, a material heat exchanger is a device specifically engineered to transfer heat between two or more fluids without them mixing. Its operation is predicated on principles of thermodynamics, wherein thermal energy from a high-temperature medium is transferred to a lower-temperature medium, leading to a host of functional efficiencies.
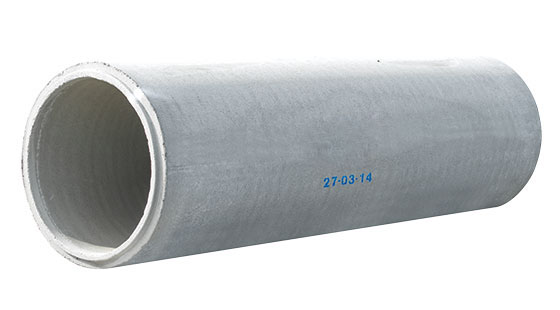
Technological advancements have brought about revolutionary materials and designs in heat exchangers, enhancing performance across diverse sectors like HVAC, automotive, power generation, and chemical processing. Stainless steel, copper, aluminum, and even advanced ceramics are frequently utilized in constructing these devices, each offering unique benefits. The choice of material is paramount; it dictates the heat exchanger's thermal conductivity, corrosion resistance, and mechanical robustness, ultimately impacting longevity and cost-effectiveness.
From an experiential standpoint, industries have gleaned valuable insights into optimizing material heat exchangers for maximum efficacy. Companies have witnessed substantial decreases in energy expenditures through investment in high-efficiency exchangers, crafted from state-of-the-art materials. For instance, the HVAC sector has benefited from copper's superior thermal conductivity and corrosion resistance, leading to enhanced heat transfer rates and operational efficiency in cooling systems.
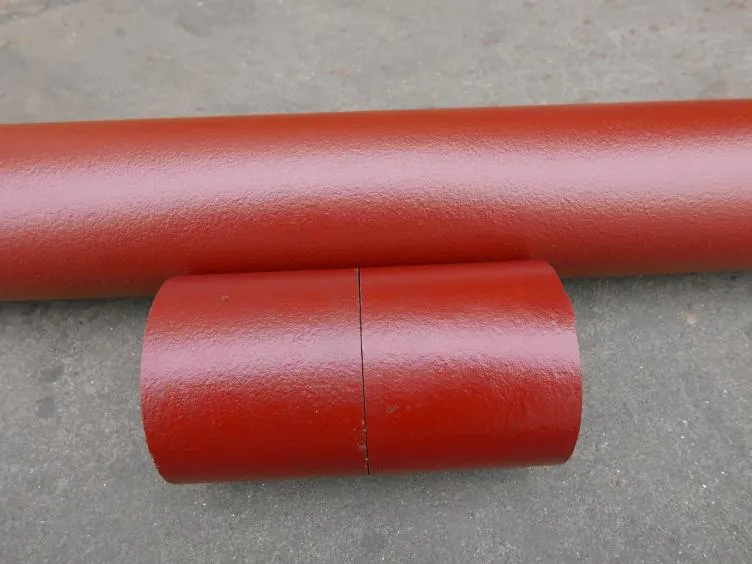
Analyzing these applications through an expert lens reveals a symbiosis between innovative material choice and exchanger performance. The precision in engineering and material science manifests into pragmatic solutions - enhancing thermal performance while maintaining structural integrity. The nuanced understanding of fluid dynamics and thermal transfer principles allows experts to tailor heat exchanger designs that meet specific industrial demands, whether optimizing for weight, thermal efficiency, or maintenance requirements.
Authoritativeness in the heat exchanger arena is defined by robust technological research and development collaborations. Leading manufacturers often partner with academic institutions to push the boundaries of material science. For example, the integration of nanomaterials has opened new frontiers in heat exchanger efficiency, exhibiting extraordinary thermal properties that outperform traditional materials. Institutions such as MIT and Caltech have been at the forefront, driving fundamental discoveries and validating these technologies in real-world applications.
material heat exchanger
Trustworthiness in the deployment of material heat exchangers is built on rigorous testing and quality assurance protocols. Industry standards such as those set by the American Society of Mechanical Engineers (ASME) provide a benchmark against which exchanger performance and safety can be gauged. Manufacturers committed to these standards ensure that their products can withstand the rigors of industrial applications, offering clients peace of mind and assurance of reliability.
Furthermore, real-world case studies exemplify the tangible benefits of deploying advanced material heat exchangers. In a case involving a major petrochemical plant, the integration of titanium-based exchangers led to a direct 25% reduction in energy consumption and a marked decrease in downtime due to exchanger fouling. This exemplifies the potential of material innovation to mitigate operational challenges while offering economic advantages.
In the competitive landscape of industrial applications, the adoption of cutting-edge material heat exchangers stands as a testament to an organization’s commitment to sustainability and efficiency. As awareness around environmental impact and energy conservation intensifies, businesses are increasingly recognizing the critical role that technologically advanced heat exchangers play in achieving these objectives.
Material heat exchangers represent more than just novel engineering components; they signify a convergence of science, industry, and environmental stewardship. The ongoing evolution in materials and design methodologies promises a future of enhanced energy efficiencies and operational resilience, driven by expert innovation and authoritative research. Trust in these technologies will continue to grow as they prove their worth in diverse applications, cementing their place as indispensable tools in the industrial toolkit.