The Art and Science of Casting Metal Supply
Casting metal supply is a crucial aspect of the manufacturing industry, as it involves the production of various metal parts and components that are used in a wide range of applications. From automotive to aerospace, from construction to consumer goods, casting metal supply plays a vital role in ensuring the smooth functioning of these industries.
The process of casting metal supply begins with the selection of appropriate metals based on their properties, such as strength, durability, and resistance to corrosion. Common metals used in casting include aluminum, bronze, brass, iron, steel, and titanium. Once the metal is chosen, it is melted down and poured into molds or dies to create the desired shape. This can be done through various methods, such as sand casting, die casting, investment casting, or lost foam casting.
Sand casting is one of the oldest and most versatile methods of casting metal supply. It involves creating a mold using sand mixed with a binder, which is then filled with molten metal. The advantage of sand casting is its ability to produce complex shapes and large sizes at a relatively low cost. However, it may not be suitable for high-precision applications due to its lower accuracy compared to other casting methods.
Die casting, on the other hand, is a more precise method that involves injecting molten metal under high pressure into reusable metal dies. This results in high-quality, consistent parts with smooth surfaces and tight tolerances. Die casting is commonly used for producing small to medium-sized parts with intricate details, such as automotive engine components or electronic housings Die casting is commonly used for producing small to medium-sized parts with intricate details, such as automotive engine components or electronic housings
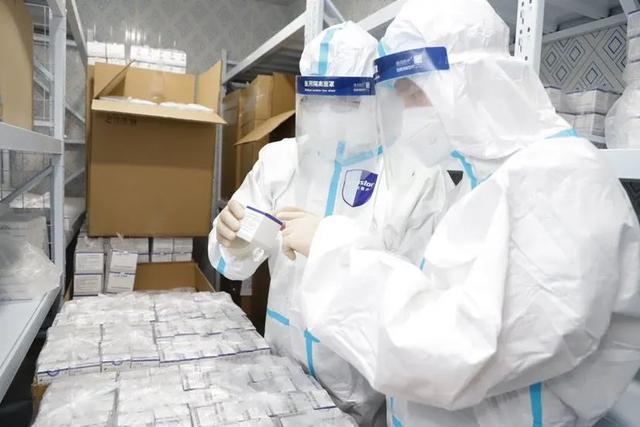
Die casting is commonly used for producing small to medium-sized parts with intricate details, such as automotive engine components or electronic housings Die casting is commonly used for producing small to medium-sized parts with intricate details, such as automotive engine components or electronic housings
casting metal supply.
Investment casting, also known as lost wax casting, is another precision method that involves creating a wax model of the desired part, which is then coated with a refractory material and baked to form a ceramic shell. The shell is then heated to remove the wax and filled with molten metal. This method allows for very fine details and thin walls, making it ideal for producing jewelry, dental implants, or aircraft engine parts.
Lost foam casting is a relatively new method that combines the advantages of both sand casting and investment casting. It involves creating an expandable polystyrene foam pattern of the desired part, which is then coated with a refractory material and baked to form a ceramic shell. The shell is then filled with molten metal, which vaporizes the foam pattern and creates a precise replica of the original pattern. This method offers the benefits of low cost, high accuracy, and the ability to produce complex shapes without the need for expensive tooling.
In conclusion, casting metal supply is a complex and diverse field that requires a deep understanding of materials science, engineering principles, and manufacturing processes. By selecting the appropriate metal and casting method based on the specific requirements of each application, manufacturers can ensure the production of high-quality parts that meet their performance needs while minimizing costs and maximizing efficiency. As technology continues to advance and new materials and techniques emerge, the art and science of casting metal supply will undoubtedly evolve further, opening up exciting possibilities for innovation and improvement in various industries worldwide.