The Art and Science of High-Quality Cast Aluminum Parts
High-quality cast aluminum parts are a testament to the marriage of art and science. The process of casting aluminum into intricate shapes and functional components involves both precision engineering and creative problem-solving, making it a fascinating field for those who seek innovation in manufacturing.
The journey begins with selecting the right type of aluminum alloy. Each alloy has its unique properties that cater to specific applications, such as strength, ductility, or heat resistance. Once the alloy is chosen, the casting process can commence, which typically involves one of two primary methods sand casting or die casting.
Sand casting, often used for prototypes or small production runs, offers flexibility in design but may require more finishing work due to its inherent roughness. Die casting, on the other hand, is ideal for high-volume production since it produces precise, dimensionally accurate parts with smooth surfaces. However, it requires significant upfront investment in tooling.
Regardless of the method, the casting process must be closely monitored to ensure the quality of the final product. Temperature control is critical; too hot, and the aluminum might burn or distort; too cool, and it might not flow into the mold's finer details Temperature control is critical; too hot, and the aluminum might burn or distort; too cool, and it might not flow into the mold's finer details
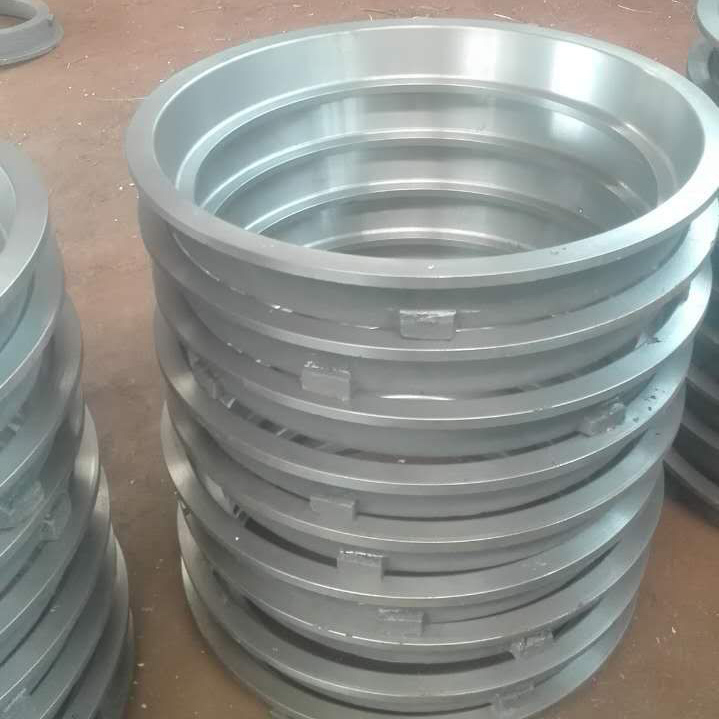
Temperature control is critical; too hot, and the aluminum might burn or distort; too cool, and it might not flow into the mold's finer details Temperature control is critical; too hot, and the aluminum might burn or distort; too cool, and it might not flow into the mold's finer details
high quality cast aluminum parts casting. Additionally, the cooling rate must be carefully managed to prevent defects like porosity or uneven microstructures.
After casting, each part undergoes rigorous inspection to meet stringent quality standards. This includes visual checks for any surface imperfections, dimensional measurements to confirm tolerances, and sometimes non-destructive testing (NDT) to identify internal flaws. Any identified issues are then addressed through various finishing processes, such as machining, polishing, or coating.
In conclusion, high-quality cast aluminum parts are the result of a delicate balance between material selection, casting technique, process control, and post-casting inspections. They serve as a testament to human ingenuity and the endless possibilities that arise when we blend scientific principles with artisanal craftsmanship. As technology advances, the potential for creating even more sophisticated and reliable cast aluminum components continues to expand, promising a future where these parts play an even greater role in shaping our world.