Understanding the OEM Bronze Investment Casting Process and Its Impact on Modern Manufacturing
Investment casting, also known as lost-wax casting, is an ancient metal forming technique that has stood the test of time and continues to play a significant role in modern manufacturing, particularly in the Original Equipment Manufacturer (OEM) sector. When it comes to bronze, this method offers a unique blend of precision, versatility, and durability, making bronze investment casting a preferred choice for various industries.
Bronze, a metal alloy primarily composed of copper and tin, has been used for centuries due to its strength, corrosion resistance, and aesthetic appeal. The investment casting process for bronze involves several intricate steps, each contributing to the final product's quality and accuracy.
Firstly, a wax or plastic pattern is created in the desired shape of the final component. This pattern is then coated with a refractory ceramic material, building up multiple layers to form a mold. Once the mold is complete, the wax or plastic is melted out, leaving a hollow cavity in the shape of the part. This is where the lost-wax term comes from.
The next step is to pour molten bronze into the empty mold cavity. As the bronze cools and solidifies, it assumes the exact shape of the original pattern. The ceramic shell is then carefully broken away, revealing the cast bronze component. The part undergoes post-casting operations like machining, heat treatment, and surface finishing to meet specific customer requirements The part undergoes post-casting operations like machining, heat treatment, and surface finishing to meet specific customer requirements
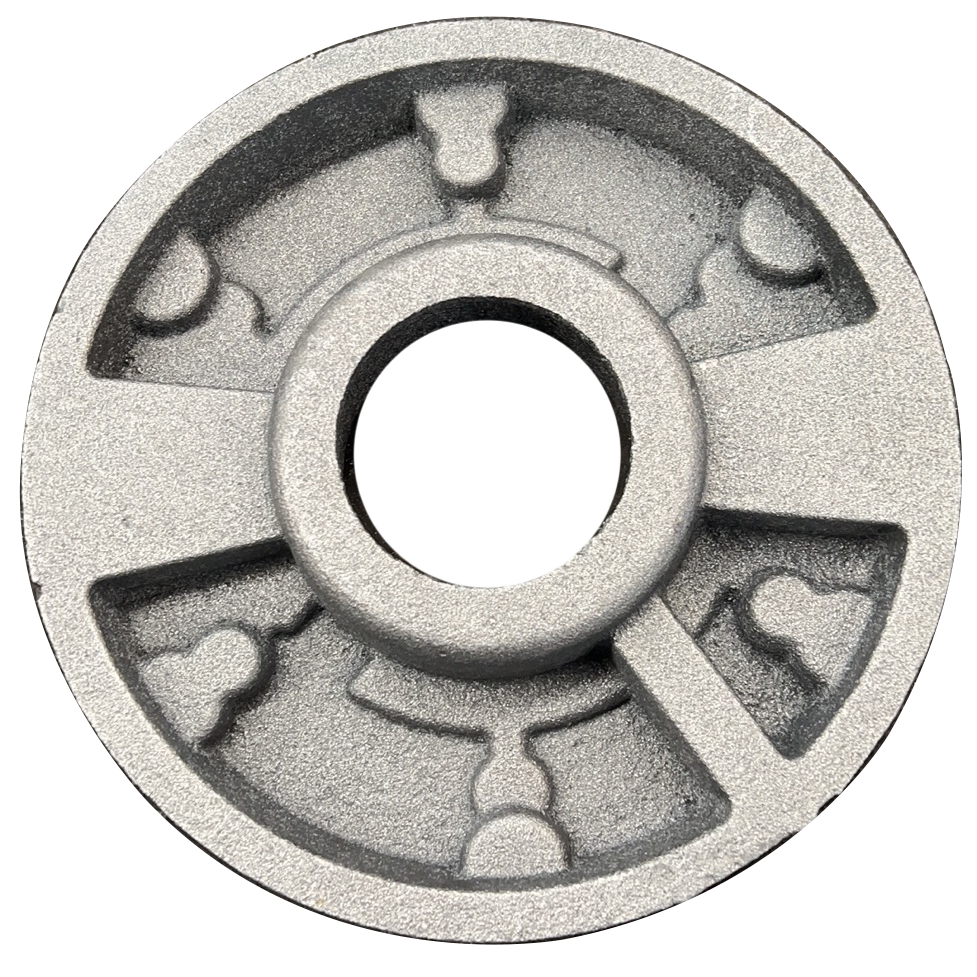
The part undergoes post-casting operations like machining, heat treatment, and surface finishing to meet specific customer requirements The part undergoes post-casting operations like machining, heat treatment, and surface finishing to meet specific customer requirements
oem bronze investment casting.
In the context of OEMs, bronze investment casting offers several advantages. It allows for the creation of complex geometries with exceptional detail, making it ideal for producing components with intricate designs. The process also enables the production of small batches or large-scale runs with minimal waste, thus providing cost-effectiveness. Moreover, the inherent properties of bronze, such as high strength-to-weight ratio and excellent wear resistance, make it suitable for applications in automotive, marine, aerospace, and architectural industries.
One notable application of OEM bronze investment casting is in the production of high-stress mechanical parts, like bearings, gears, and valves. These components require precise dimensions and consistent performance, which the investment casting process can deliver reliably. Additionally, bronze's non-sparking nature makes it ideal for use in hazardous environments.
In conclusion, the OEM bronze investment casting process is a testament to the fusion of traditional craftsmanship and modern technology. It offers manufacturers the ability to create high-quality, durable, and intricate components, while maintaining efficiency and cost-effectiveness. As the manufacturing landscape continues to evolve, bronze investment casting remains a valuable tool in the production of diverse and specialized components across various industries.