Understanding Heat Exchanger Sizing A Comprehensive Guide
Heat exchangers play an integral role in numerous industrial processes, where efficient heat transfer between two fluids is vital for process optimization and energy conservation. The sizing of a heat exchanger is a critical aspect of its design,、。 This article delves into the fundamental principles and considerations involved in heat exchanger sizing, providing a comprehensive guide for engineers and professionals in the field.
**Fundamentals of Heat Exchanger Sizing**
Heat exchanger sizing involves determining the optimal dimensions, such as the surface area (A), and other design parameters like flow rates, pressures, and temperatures, to ensure effective heat transfer while meeting specific process requirements. The primary goal is to achieve the desired heat transfer rate (Q) with an acceptable pressure drop and efficiency.
**Key Parameters and Formulas**
The sizing process revolves around several key variables
1. **Heat Transfer Rate (Q)** This is the amount of heat to be transferred between the hot and cold fluids. It can be calculated using the formula
\[Q = U \times A \times \Delta T_{LM}\]
Where
- \(U\) is the overall heat transfer coefficient.
- \(A\) is the heat transfer surface area.
- \(\Delta T_{LM}\) is the log mean temperature difference between the hot and cold fluids.
2. **Overall Heat Transfer Coefficient (U)** This combines the effects of conduction, convection, and any fouling resistance. Its value depends on the type of heat exchanger, fluid properties, and flow conditions.
3. **Log Mean Temperature Difference (\(\Delta T_{LM}\))** This represents the average temperature difference between the hot and cold fluids and is crucial for calculating heat transfer. It's calculated based on inlet and outlet temperatures of both fluids.
4. **Pressure Drop** Maintaining acceptable pressure drops across the exchanger is important to avoid excessive pumping costs. This is typically estimated using fluid dynamics equations.
**Design Considerations**
1. **Type of Heat Exchanger** There are various types, including shell-and-tube, plate, and spiral, each suited for different applications. The selection impacts the sizing calculations significantly.
2. **Fluid Properties** Viscosity, density, specific heat, and thermal conductivity of the fluids influence heat transfer and pressure drop calculations.
3. **Flow Arrangement** Counterflow, parallel flow, or crossflow configurations affect the temperature profiles and thus, the \(\Delta T_{LM}\) **Flow Arrangement** Counterflow, parallel flow, or crossflow configurations affect the temperature profiles and thus, the \(\Delta T_{LM}\)
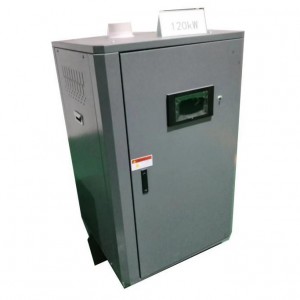
**Flow Arrangement** Counterflow, parallel flow, or crossflow configurations affect the temperature profiles and thus, the \(\Delta T_{LM}\) **Flow Arrangement** Counterflow, parallel flow, or crossflow configurations affect the temperature profiles and thus, the \(\Delta T_{LM}\)
heat exchanger sizing.
4. **Fouling Factors** Over time, deposits can accumulate on heat transfer surfaces, reducing efficiency. Incorporating fouling factors in the U-value ensures realistic performance estimates.
5. **Economic and Safety Factors** While maximizing heat transfer efficiency, designers must also consider capital costs, maintenance requirements, and safety standards.
**Sizing Procedure**
1. **Define Process Requirements** Clearly outline the heat load (Q), inlet and outlet temperatures, flow rates, and allowable pressure drops.
2. **Select Heat Exchanger Type** Based on process specifics, choose the most suitable heat exchanger design.
3. **Estimate U-Value** Gather data on fluid properties and expected fouling rates to calculate U.
4. **Calculate ΔTLM** Use inlet and outlet temperatures to determine the log mean temperature difference.
5. **Determine Surface Area (A)** Rearrange the heat transfer formula to solve for A, ensuring it meets all design constraints.
6. **Pressure Drop Analysis** Validate that the designed exchanger does not induce excessive pressure drops.
7. **Iterate and Optimize** Adjust parameters iteratively until an optimal balance between heat transfer efficiency, cost, and operational feasibility is achieved.
**Conclusion**
Heat exchanger sizing is a meticulous process requiring a deep understanding of thermodynamics, fluid mechanics, and practical engineering considerations. By meticulously following the outlined steps and considering all influencing factors, engineers can design heat exchangers that not only meet performance expectations but also contribute to overall system efficiency and cost-effectiveness. Continuous technological advancements and computational tools are further enhancing the precision and speed of heat exchanger sizing, making it an ever-evolving art in engineering design.