The Evolution of Precision Investment Casting in Rion's Factories
In the heart of industrial innovation, Rion's factories stand as a testament to the relentless pursuit of perfection in precision investment casting. This advanced manufacturing technique has revolutionized the production process, enabling the creation of high-integrity, complex parts with exceptional dimensional accuracy and surface finish.
The journey of precision investment casting at Rion begins with the art of wax modeling. Skilled artisans craft intricate wax patterns that serve as blueprints for the metal components to come. These models are not mere representations; they embody the essence of precision, ensuring that every detail is captured with exactitude.
Transitioning from wax to metal involves a meticulous process known as shell building. Layer upon layer of refractory slurry is carefully applied over the wax patterns, building a robust, yet delicate, ceramic shell. Once cured, the shell undergoes a thermal process called dewaxing, where the wax is melted away, leaving behind a negative impression in the ceramic mold.
The true alchemy occurs in the furnace, where the empty shells are filled with molten metal, a step termed as burn-out and casting. The metal seeps into the finest crevices, replacing the void left by the departed wax. As it solidifies, the metal assumes the precise shape and texture intended by the original wax model, demonstrating the remarkable fidelity of this transformation process As it solidifies, the metal assumes the precise shape and texture intended by the original wax model, demonstrating the remarkable fidelity of this transformation process
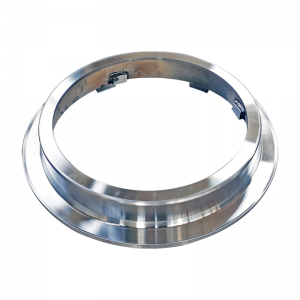
As it solidifies, the metal assumes the precise shape and texture intended by the original wax model, demonstrating the remarkable fidelity of this transformation process As it solidifies, the metal assumes the precise shape and texture intended by the original wax model, demonstrating the remarkable fidelity of this transformation process
precision cast rion casting factories.
Post-casting, the ceramic shell is removed through a process akin to unwrapping a delicate gift, revealing the finely cast metal part inside. However, the journey to perfection is not yet complete. The castings undergo rigorous finishing processes—from grit blasting to remove any remaining ceramic remnants, to hand polishing for an immaculate surface quality.
Quality control at Rion’s factories is a narrative of its own. Each casting is inspected using state-of-the-art equipment to ensure it meets stringent standards before it leaves the facility. From micrometer measurements to X-ray inspections, no stone is left unturned in guaranteeing the superior performance of each component.
In conclusion, Rion's precision investment casting factories epitomize the synergy of artistry and engineering. They produce not just metal parts but sculptures in metal, each one a masterpiece of precision and reliability. As technology evolves, so too does the capability of these factories, promising a future where the limits of precision investment casting are constantly redefined.