Investment Casting Parts Manufacturer Unleashing Precision and Efficiency in Modern Manufacturing
In the realm of precision engineering and manufacturing, investment casting, also known as lost-wax casting, stands as a cornerstone technique, revered for its ability to produce intricate and exact components across diverse industries. As technology advances, the role of a proficient investment casting parts manufacturer has become increasingly vital, catering to the stringent demands of sectors such as aerospace, automotive, medical, and defense, where accuracy and reliability are paramount.
**The Art and Science Behind Investment Casting**
Investment casting owes its prowess to an age-old process that combines artistry with advanced materials science. It begins with creating a wax or plastic pattern, intricately designed to mirror the final part's shape. This pattern is then coated with several layers of ceramic slurry, allowing it to solidify into a robust mold. Once the mold is heated, the wax melts and is drained out, leaving a hollow cavity in the exact form of the desired component. Molten metal is subsequently poured into this cavity, cooled, and solidifies, after which the ceramic shell is broken away, revealing the finished casting.
**Precision Engineering for Demanding Industries**
The allure of investment casting lies in its capability to fabricate complex shapes with remarkable accuracy and consistency, often eliminating the need for secondary machining processes. Aerospace manufacturers, for instance, rely heavily on investment cast parts for turbine blades, engine components, and airframe structures that must withstand extreme temperatures and stresses while maintaining feather-light weight and optimal performance. Similarly, in the medical industry, the production of precise surgical instruments and implants necessitates the use of this technique to ensure biocompatibility and functionality.
**Innovation Driving Competitive Advantage**
A leading investment casting parts manufacturer is one that constantly pushes the boundaries of technology and material science. This includes adopting computer-aided design (CAD) and 3D printing for pattern creation, enabling faster prototyping and customization. Advanced simulation software further enhances the process, predicting and mitigating potential casting defects before production, thereby reducing waste and optimizing efficiency Advanced simulation software further enhances the process, predicting and mitigating potential casting defects before production, thereby reducing waste and optimizing efficiency
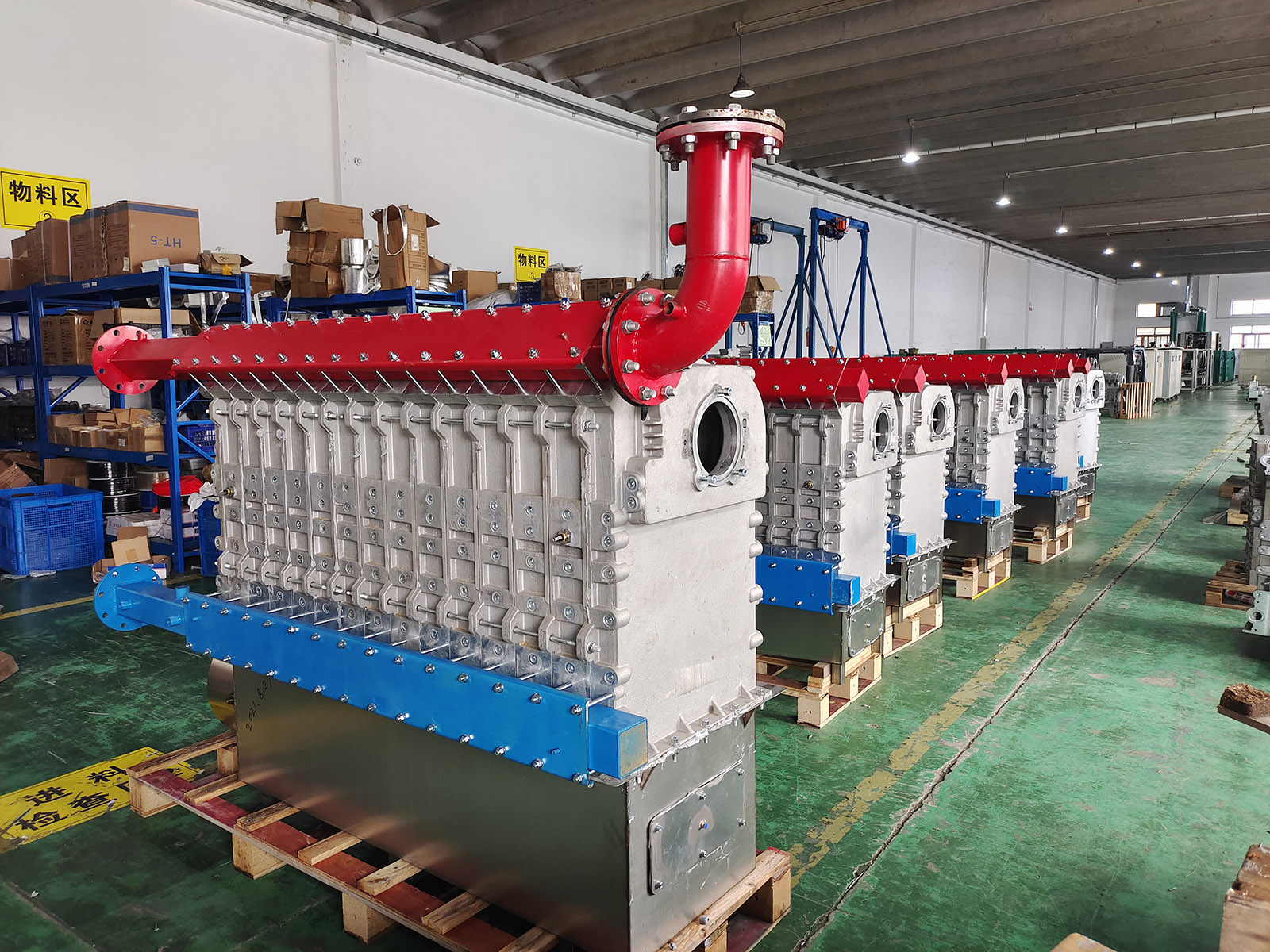
Advanced simulation software further enhances the process, predicting and mitigating potential casting defects before production, thereby reducing waste and optimizing efficiency Advanced simulation software further enhances the process, predicting and mitigating potential casting defects before production, thereby reducing waste and optimizing efficiency
investment casting parts manufacturer.
Moreover, these manufacturers are exploring new alloys and composite materials to meet the ever-evolving demands for lighter, stronger, and more corrosion-resistant parts. Materials like titanium and its alloys, known for their superior strength-to-weight ratio, are increasingly favored in high-performance applications, necessitating expertise in handling these challenging metals.
**Quality Assurance A Cornerstone of Trust**
In an industry where even the slightest deviation can lead to catastrophic failures, quality control is not just a process—it’s a culture. Top-tier manufacturers implement rigorous inspection protocols at every stage, from raw material sourcing to final product testing. Non-destructive testing (NDT) methods such as X-ray radiography, ultrasonic testing, and magnetic particle inspection are employed to detect internal defects invisible to the naked eye, ensuring compliance with international standards and customer specifications.
**Sustainability in Manufacturing**
As global consciousness shifts towards sustainable practices, environmentally conscious investment casting manufacturers are adopting green initiatives. This includes recycling of materials like wax, ceramic shells, and metal scraps, reducing energy consumption through efficient furnace designs, and implementing wastewater treatment systems to minimize environmental impact.
**Conclusion**
In conclusion, the world of investment casting parts manufacturing is a testament to human ingenuity and technological progress. It serves as a cornerstone for advancements across multiple sectors, delivering components that are not just parts but integral to pushing the limits of innovation. As industries continue to demand higher precision, durability, and adaptability, the role of skilled investment casting manufacturers will only grow more pivotal, shaping the future of manufacturing with precision and efficiency at its core.