Sand casting, an ancient metalworking process, has been a cornerstone of manufacturing for centuries. In sand casting parts factories, the art and science of transforming molten metal into precise components is practiced with precision and care. These facilities are not just places where metal meets sand; they are hubs of innovation, where raw materials are shaped into the building blocks of modern industry.
The process itself begins with the creation of a pattern, which is used to make a mold. This pattern is typically crafted from wood or metal and serves as the blueprint for the part to be cast. The mold is then formed around this pattern using a special mixture of sand and a binding agent. Once the mold is prepared, it's time for the molten metal to take center stage.
As the metal is poured into the carefully constructed sand mold, a symphony of hisses and pops fills the air. The heat is intense, but the sand holds firm, containing the shape of the future part. After cooling and solidifying, the sand mold is broken away to reveal the newly cast part, often requiring further refinement through processes like grinding or machining.
In these factories, each step in the sand casting process is optimized for efficiency and quality. From the selection of the right type of sand to the precise control of metal temperatures, every detail is meticulously managed From the selection of the right type of sand to the precise control of metal temperatures, every detail is meticulously managed
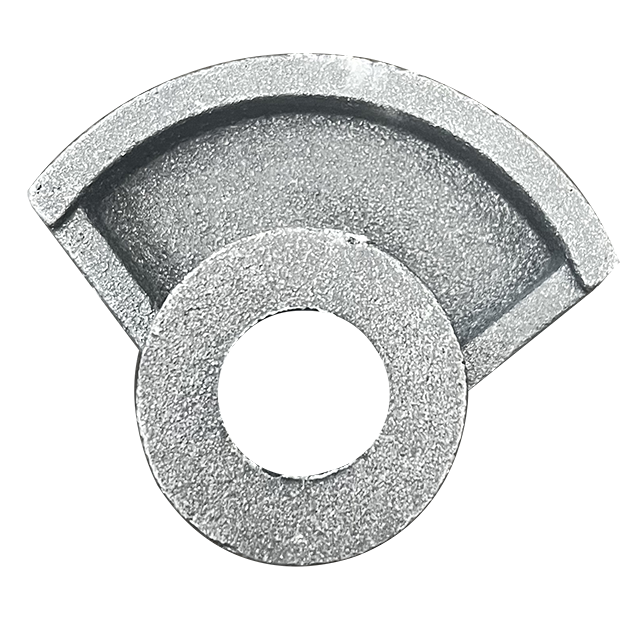
From the selection of the right type of sand to the precise control of metal temperatures, every detail is meticulously managed From the selection of the right type of sand to the precise control of metal temperatures, every detail is meticulously managed
sand casting parts factories. The sand used is often a mix of silica sand, which can withstand high temperatures without breaking down, and various additives that enhance its performance.
Moreover, sand casting parts factories have embraced technological advancements to improve their output. Computer-aided design (CAD) allows for more accurate patterns, while computer-aided manufacturing (CAM) automates some of the finishing processes. These technologies reduce errors, save time, and lower costs, making sand casting a competitive option for producing complex shapes and large quantities.
Despite being an older method compared to newer manufacturing techniques like 3D printing, sand casting remains relevant due to its ability to produce large parts with intricate details. It's also cost-effective for low-volume production runs, making it a go-to method for custom work.
In conclusion, sand casting parts factories are dynamic environments where craftsmanship meets technology, and tradition blends with innovation. They play a vital role in supplying the machinery, tools, and parts that drive industries forward. As long as there is a need for strong, durable metal components with complex geometries, these factories will continue to churn out essential elements that keep the gears of progress turning.