The Art and Science of Casting Aluminum Alloys
Casting aluminum alloys is a sophisticated blend of art and science, where precise calculations meet the molten heat of creativity. This process begins with understanding the properties of aluminum alloys themselves. These alloys, composed mainly of aluminum with other elements such as copper, zinc, silicon, magnesium, or manganese, offer a variety of benefits including low density, high strength to weight ratio, and excellent corrosion resistance.
The casting process itself is a testament to human innovation. It starts with the preparation of the mold, which can be made from various materials like sand, metal, or even graphite. The choice of mold material often depends on the complexity of the desired end product and the number of duplicates needed. Sand casting, for instance, is favored for complex shapes and low volume production, while die-casting excels in producing high volumes of smaller, less intricate items.
Once the mold is prepared, it's time for the heart of the process – melting and pouring the aluminum alloy. The alloy is melted in a furnace, typically reaching temperatures between 700 to 800 degrees Celsius. The molten metal must then be carefully transferred and poured into the waiting mold. This step requires both precision and speed to ensure the metal doesn't cool prematurely and to avoid turbulence that might introduce air bubbles or imperfections This step requires both precision and speed to ensure the metal doesn't cool prematurely and to avoid turbulence that might introduce air bubbles or imperfections
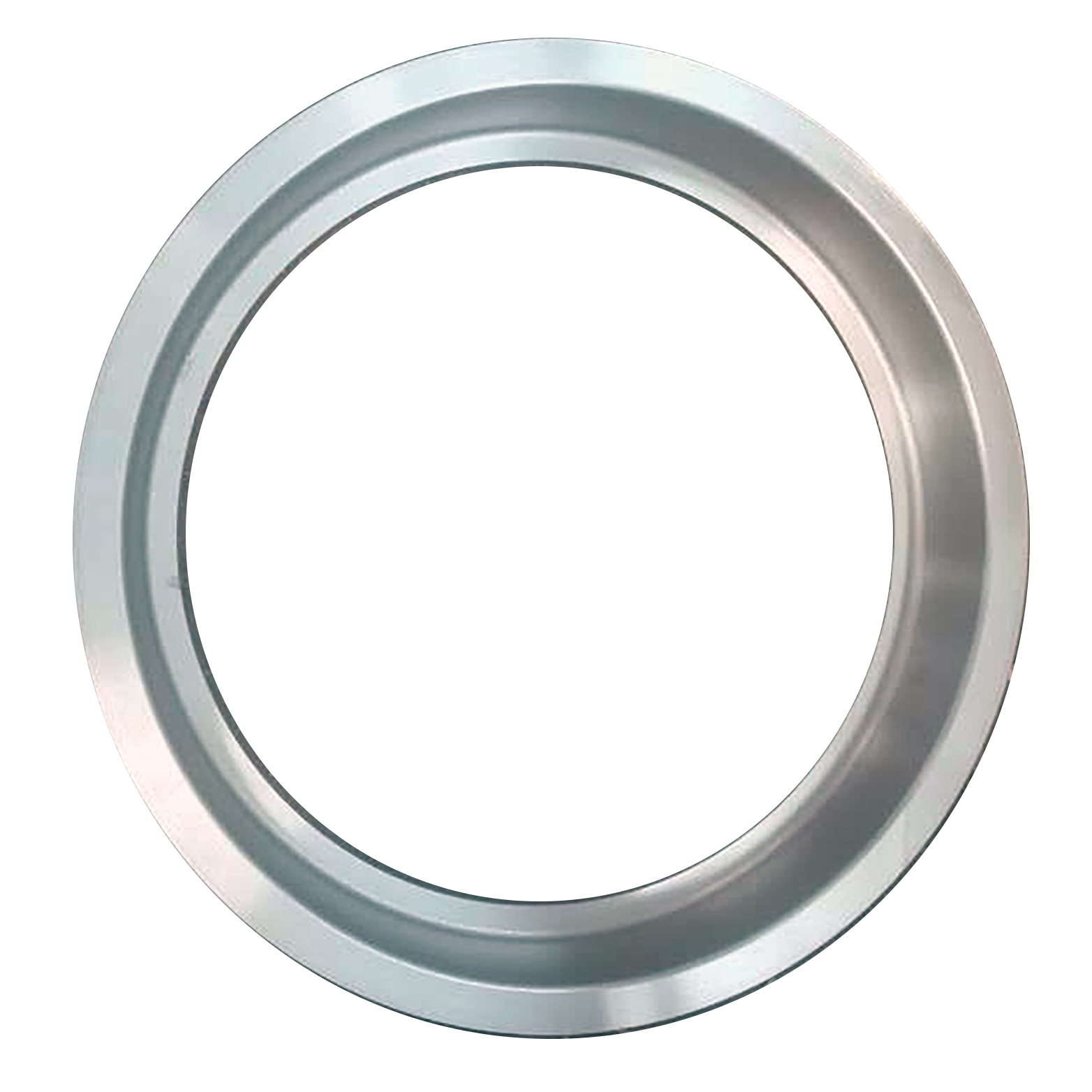
This step requires both precision and speed to ensure the metal doesn't cool prematurely and to avoid turbulence that might introduce air bubbles or imperfections This step requires both precision and speed to ensure the metal doesn't cool prematurely and to avoid turbulence that might introduce air bubbles or imperfections
casting aluminum alloys.
After pouring, the metal is left to cool and solidify within the mold. The cooling rate is crucial; too fast, and internal stresses can fracture the casting, but too slow, and the grain structure might become coarse, affecting the alloy's mechanical properties. Upon reaching the right temperature, the mold is opened, and the casting is removed. However, this is just the beginning of the journey for the newly cast aluminum alloy part.
Post-casting processes like deburring, where excess metal attached to the casting is removed, and heat treatment, used to improve strength and ductility, further refine the product. Heat treatment can involve processes such as annealing, where the alloy is heated and slowly cooled to soften it, or age hardening, which enhances strength and hardness by precipitating tiny particles within the alloy's structure.
In summary, the process of casting aluminum alloys is a meticulous dance involving the careful selection of materials, precise control over temperatures, and a deep understanding of how different alloys behave under various conditions. It's an intersection of technology and chemistry that yields not only functional components but also pieces of art—each casting a unique manifestation of human innovation harnessed through scientific principles.