The Significance of Silica Sol Casting Factories in Modern Manufacturing
Silica sol casting, a specialized process in the metallurgical industry, has emerged as a pivotal technique in the production of high-precision metal components. This method is widely employed by factories worldwide due to its ability to create intricate shapes with exceptional accuracy and surface finish.
Silica sol casting factories are the backbone of this sophisticated manufacturing process. These facilities are equipped with cutting-edge technology and skilled labor, ensuring the production of parts that meet stringent quality standards. The term 'silica sol' refers to a colloidal solution of fine silica particles suspended in water, which serves as a binding agent in the mold-making stage.
The process begins with the preparation of the silica sol. In the factory, this involves mixing silica powder with water and an acid or alkali to form a stable suspension. The resulting sol is then applied to a pattern, creating a thin, hard shell when it dries. This shell, once hardened, becomes the mold for the metal casting. The precision of this method lies in the minute size of the silica particles, enabling the creation of complex geometries with minute details.
Silica sol casting factories play a crucial role in industries like aerospace, automotive, and medical devices where parts need to be both strong and dimensionally accurate. The automotive sector, for instance, benefits from the production of lightweight yet durable engine components. In aerospace, silica sol casting is used for manufacturing intricate parts for engines and aircraft structures, ensuring safety and performance In aerospace, silica sol casting is used for manufacturing intricate parts for engines and aircraft structures, ensuring safety and performance
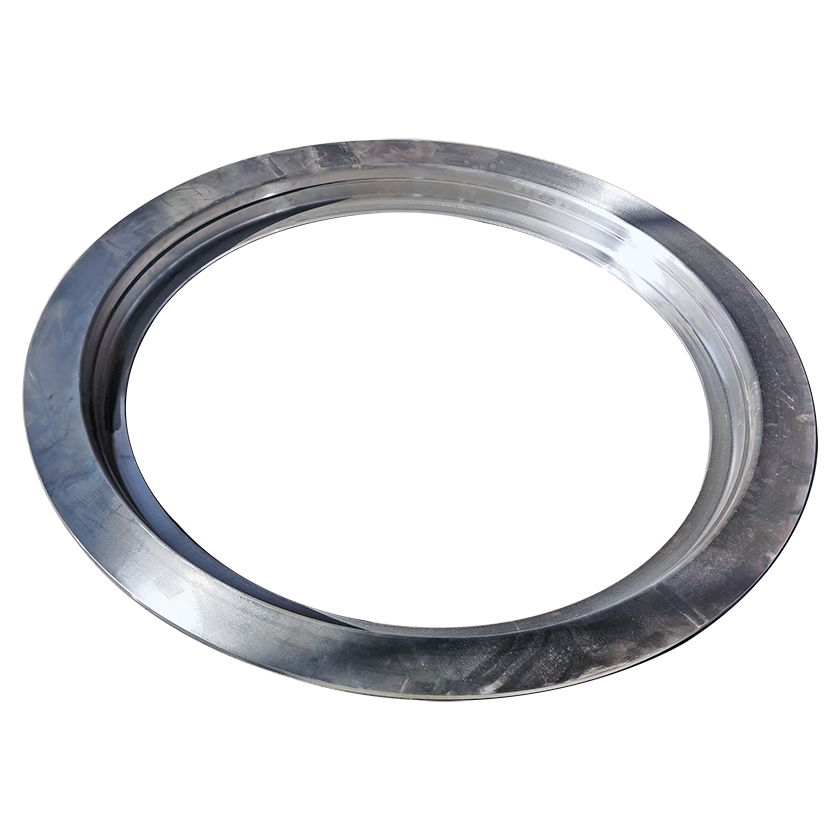
In aerospace, silica sol casting is used for manufacturing intricate parts for engines and aircraft structures, ensuring safety and performance In aerospace, silica sol casting is used for manufacturing intricate parts for engines and aircraft structures, ensuring safety and performance
silica sol casting factories.
Moreover, these factories also emphasize sustainability. The process allows for minimal waste generation, as the silica sol can be recycled, reducing environmental impact. Furthermore, the high accuracy reduces the need for post-processing, saving energy and resources.
However, operating a silica sol casting factory requires stringent quality control measures. The controlled environment, precise temperature and humidity conditions, and careful monitoring of the sol's properties are all critical factors. Skilled technicians and engineers work tirelessly to ensure each step of the process adheres to strict standards.
In conclusion, silica sol casting factories are more than just manufacturing units; they are centers of innovation and precision engineering. They embody the marriage of science and technology, pushing the boundaries of what can be achieved in metal casting. As we move towards a future that demands higher precision and efficiency, the significance of these factories will only continue to grow. Their role in shaping the modern industrial landscape cannot be overstated, making them a vital part of our global manufacturing network.