The Fascinating World of Steel Casting Factories An Insight
Steel casting factories are the epitome of industrial might and innovation, playing a pivotal role in shaping our modern world. These mammoth facilities, with their intricate processes and towering furnaces, turn raw materials into the durable, resilient steel that forms the backbone of countless structures, vehicles, and machinery.
The steel casting process begins with the melting of iron ore, coke, and limestone in a blast furnace. This intense heat, reaching up to 1,600 degrees Celsius, transforms these elements into molten iron. The liquid iron is then transferred to a basic oxygen furnace where impurities are removed, and additional elements like carbon, manganese, and nickel are added to create the desired steel composition.
Once the steel has been refined, it's time for casting. In a steel casting factory, this is achieved through a variety of techniques including sand casting, die casting, and investment casting. Sand casting, the most common method, involves creating a mold from sand and then pouring the molten steel into it. Die casting, on the other hand, uses high pressure to force the liquid metal into complex shapes. Investment casting, also known as lost-wax casting, is a more intricate process where a wax or plastic model is created, coated with ceramic, and then melted out to leave a hollow space for the steel.
Steel casting factories are not just about brute force; they are also centers of precision engineering. Sophisticated computer-aided design (CAD) and manufacturing (CAM) systems are employed to ensure accuracy and efficiency Sophisticated computer-aided design (CAD) and manufacturing (CAM) systems are employed to ensure accuracy and efficiency
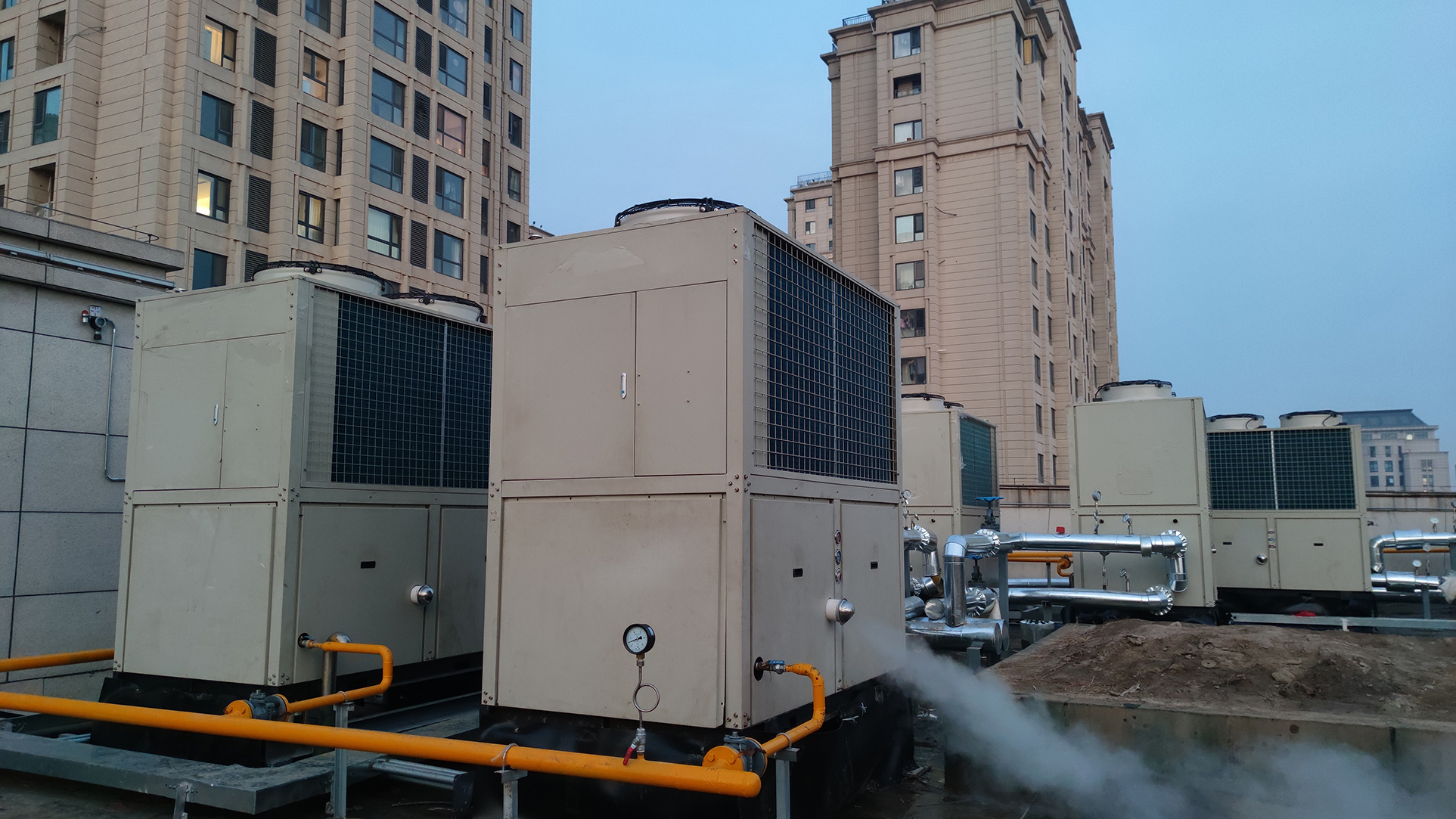
Sophisticated computer-aided design (CAD) and manufacturing (CAM) systems are employed to ensure accuracy and efficiency Sophisticated computer-aided design (CAD) and manufacturing (CAM) systems are employed to ensure accuracy and efficiency
steel casting factories. Quality control is paramount, with rigorous testing procedures to check the strength, durability, and chemical composition of the final product.
These factories are also at the forefront of sustainability efforts. They recycle scrap steel, reducing waste and the need for new raw materials. Additionally, advancements in energy-efficient technologies and emissions control systems are constantly being implemented to minimize environmental impact.
Despite their size and intensity, steel casting factories are a testament to human ingenuity and the power of industry. They symbolize progress, resilience, and the capacity to transform natural resources into the tools that build our cities, bridges, and machines. From the towering skyscrapers to the humblest household appliances, the products of steel casting factories are an integral part of our daily lives.
In conclusion, the world of steel casting factories is a dynamic blend of tradition and technology, strength and sustainability. It's a world where fire and ice meet, where raw materials are transformed into the lifeblood of modern society. Each piece of steel, forged in the crucible of these factories, carries the story of human endeavor and the enduring spirit of progress.