In the realm of heat exchange technology, selecting the optimal surface area for a heat exchanger is paramount to achieving efficiency and maximizing performance. This technically intricate subject delves into the core specifications that can significantly impact the lifecycle and effectiveness of these critical components. Drawing on extensive industry expertise, we explore how precise engineering and thoughtful design can influence the overall functioning and reliability of heat exchangers.
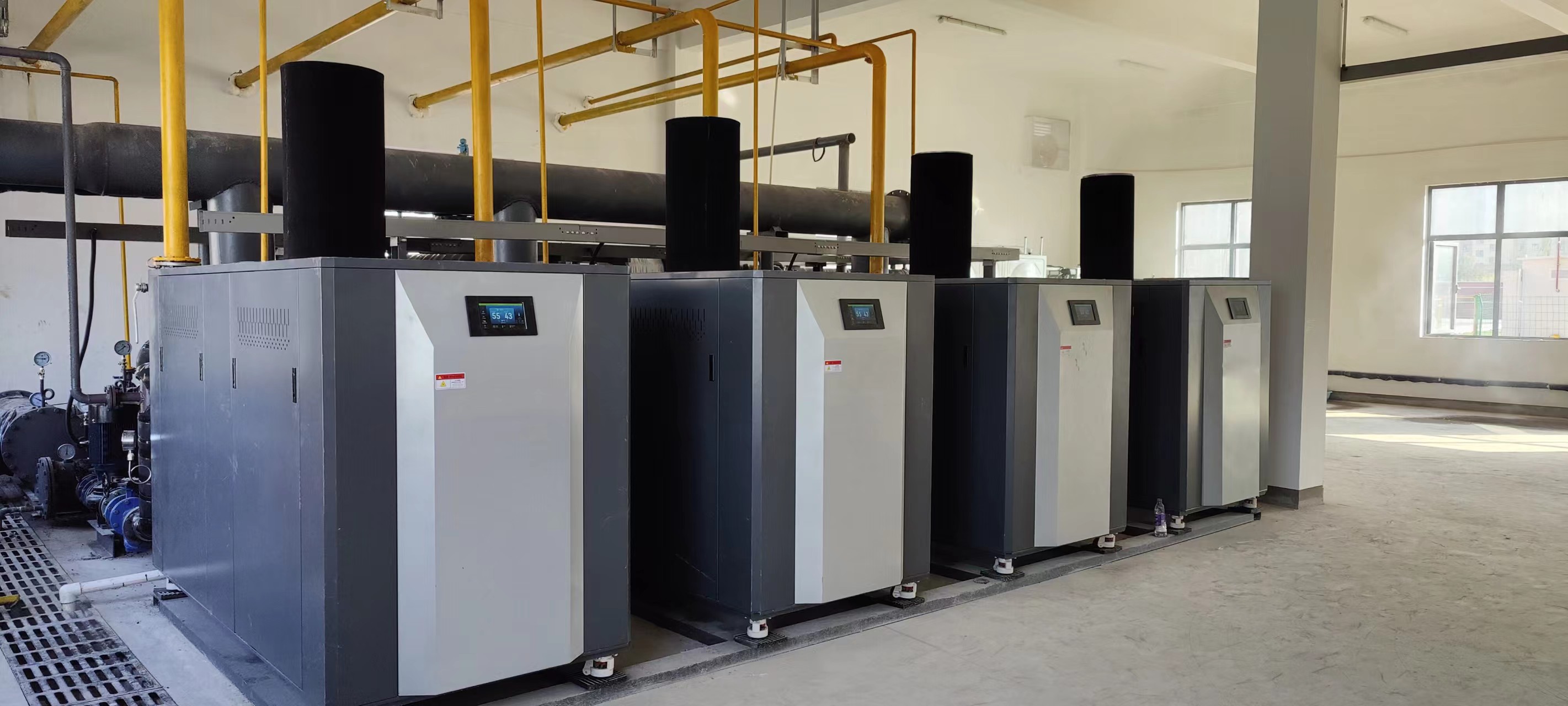
A heat exchanger's surface area plays a crucial role in the heat transfer process. Fundamentally, the surface area dictates how effectively a heat exchanger can manage the thermal energy exchange between two mediums. By examining a variety of heat exchangers utilized in different sectors including chemical processing, HVAC, and power generation, it becomes clear that the specific requirements and constraints on surface area can differ significantly based on application and performance needs.
In essence, a larger surface area facilitates enhanced heat transfer as it provides more contact space for the thermal exchange between media. This is particularly evident in shell-and-tube heat exchangers, which are a stalwart in many industrial applications. These units leverage an array of tubes housed in a shell, where the surface area is largely defined by the tube configuration - number, diameter, and length. Maximizing surface area without compromising on pressure drop or space requirements stands as a common engineering challenge.
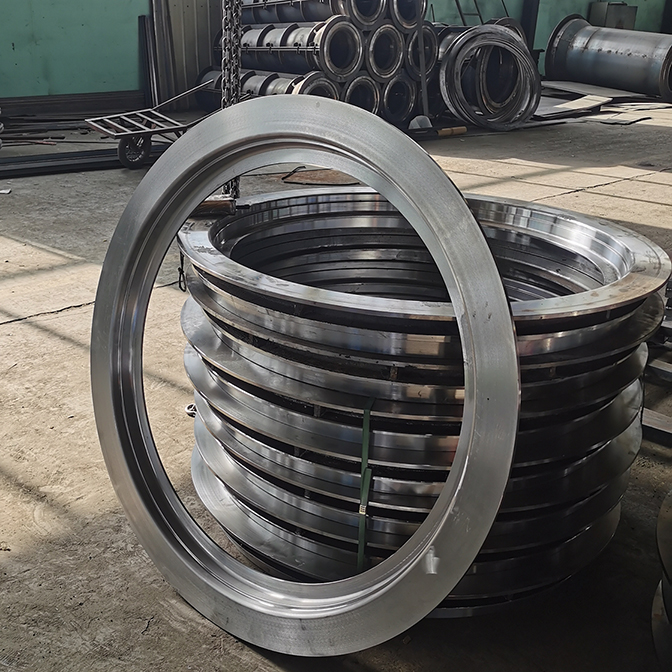
Industry expertise emphasizes the importance of customizing the heat exchanger's surface area in alignment with operational parameters such as flow rates, temperatures, pressure tolerances, and material properties. Through Computational Fluid Dynamics (CFD) simulations, engineers can model and predict the outcomes of various configurations, allowing for informed decisions that hone in on efficiency and sustainability. This not only enhances the system's energy consumption but also extends the equipment's operational life, substantiating the investment.
Despite common misconceptions,
increasing the surface area alone is not a panacea for bolstering heat exchanger performance. Oversizing can lead to increased costs, unnecessary material usage, and unwarranted complexity in maintenance operations. Therefore, it is crucial for engineers and procurement specialists to balance design with economic feasibility and operational constraints.
surface area of a heat exchanger
When assessing product enhancements or replacements, several authoritative guidelines and standards such as TEMA (Tubular Exchanger Manufacturers Association) can aid stakeholders in making educated decisions that ensure compliance and performance optimization. These standards provide comprehensive frameworks that account for material selection, mechanical design, and recommended practices, underscoring a commitment to trustworthiness and safety.
Practically, one can leverage advanced technologies such as 3D printing to manufacture heat exchangers with complex geometries that maximize surface area efficiency without excessive material use. This innovation opens avenues for custom designs tailored to specific scenarios, further supported by empirical data and real-world testing.
Moreover, regular inspections and an understanding of fouling behavior are instrumental in maintaining surface area effectiveness over time. Fouling - the accumulation of unwanted material on the heat exchange surfaces - can severely curtail performance by reducing effective surface area. Implementing a well-devised maintenance schedule coupled with materials that resist fouling can ensure the exchanger's seamless operation.
Through this lens of industry experience and authoritative insights, the selection and maintenance of a heat exchanger's surface area emerge as a multidimensional endeavor that merges engineering acumen with strategic foresight. It requires vigilance, continual adaptation, and an understanding of the interplay between physical design and process requisites. Only through such comprehensive approaches can businesses truly capitalize on the benefits offered by meticulously engineered heat exchangers, reaping advantages in operational efficiency, cost savings, and overall system reliability.