Exploring the World of Cast Iron Manufacturing A Glimpse into the Artistry and Technology Behind the Sturdy Metals
In the realm of manufacturing, few materials have stood the test of time quite like cast iron. With roots dating back to ancient China and enduring relevance in modern industry, cast iron manufacturers play a pivotal role in shaping our built environment, from cookware gracing kitchen countertops to towering structures supporting our cities. This article delves into the intricate process of cast iron production, the advancements that have revolutionized the sector, and the manufacturers leading the charge.
**The Timeless Allure of Cast Iron**
Cast iron, an alloy primarily composed of iron with 2-4% carbon content, boasts exceptional durability, heat retention, and versatility. These qualities have made it a material of choice across various sectors, including cookware, automotive, construction, and machinery parts. Its ability to withstand high temperatures and resist wear has ensured its continued relevance despite the advent of newer materials.
**The Manufacturing Process From Ore to Masterpiece**
The journey of cast iron begins at the foundry, where raw materials—primarily iron ore, coke (a fuel source), and limestone—are transformed through a series of intricate steps
1. **Melting** The raw materials are melted together in a blast furnace, reaching temperatures exceeding 1,500°C. This intense heat reduces the iron ore to liquid iron, ready for casting.
2. **Refining** Impurities are removed through a process called 'cupola melting,' where scrap iron is added to enhance the melting process and adjust the carbon content, crucial for achieving the desired properties of cast iron.
3. **Molding** The molten iron is then poured into molds, which can be made of sand, metal, or ceramic depending on the complexity and quantity required. Sand casting, a traditional method, involves packing sand around a pattern to create the mold cavity, offering great flexibility in design Sand casting, a traditional method, involves packing sand around a pattern to create the mold cavity, offering great flexibility in design
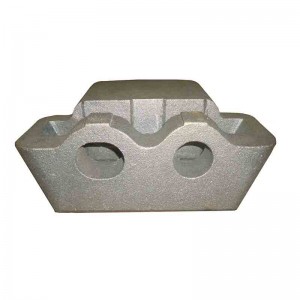
Sand casting, a traditional method, involves packing sand around a pattern to create the mold cavity, offering great flexibility in design Sand casting, a traditional method, involves packing sand around a pattern to create the mold cavity, offering great flexibility in design
cast iron manufacturer.
4. **Cooling and Finishing** Once the iron solidifies, the casting is removed from the mold and undergoes various finishing processes such as grinding, machining, and heat treatment to improve surface finish and mechanical properties.
**Technological Advancements Shaping the Industry**
In recent years, technological innovations have significantly improved the efficiency, precision, and sustainability of cast iron manufacturing
- **Computer-Aided Design (CAD) and Computer-Aided Manufacturing (CAM)** These technologies allow for intricate designs and precise mold creation, enabling manufacturers to produce complex shapes with remarkable accuracy.
- **3D Printing** Rapid prototyping using 3D printing technology speeds up the design process, reducing costs associated with traditional mold-making.
- **Automation** Automated systems for tasks such as sand preparation, molding, and pouring not only enhance productivity but also ensure consistent quality and safety in the workplace.
- **Environmental Sustainability** Manufacturers are adopting green initiatives, like recycling waste heat, using eco-friendly binders in sand casting, and optimizing resource consumption to minimize environmental impact.
**Leading Cast Iron Manufacturers Quality and Innovation**
Names like Lodge (USA), Stoveken GmbH (Germany), and Nippon Steel Corporation (Japan) stand out as global leaders in cast iron manufacturing. These companies not only excel in producing high-quality castings but also invest heavily in R&D to push the boundaries of what's possible with cast iron. Lodge, for instance, combines centuries-old casting techniques with modern technology to create iconic cookware loved worldwide.
**Conclusion**
Cast iron manufacturing, an industry steeped in history, continues to thrive through a blend of tradition and innovation. Manufacturers, leveraging advanced technologies and sustainable practices, are ensuring that this versatile material remains a cornerstone of modern industry. As we look to the future, the ongoing evolution in cast iron production promises even more efficient, precise, and environmentally friendly methods, further solidifying its position as a material of choice for generations to come.