Harnessing the power of heat for industrial applications has been a cornerstone of engineering achievements. Among the myriad technologies available, the tubular heat exchanger stands out for its efficiency and versatility in managing thermal transfer across various industries. This article delves into the world of tubular heat exchangers from a professional standpoint, exploring their design, functionality, applications, and the intrinsic advantages they offer.
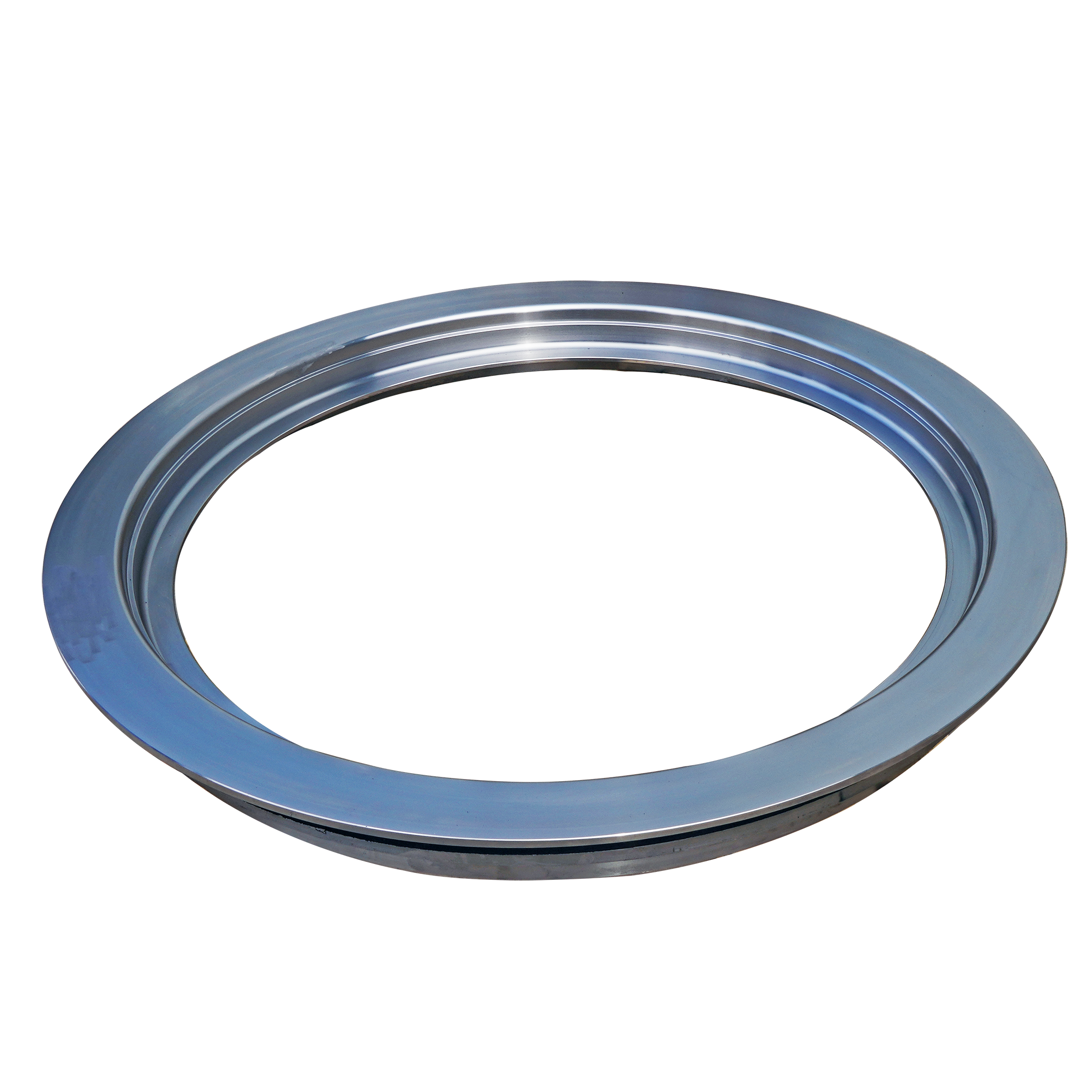
Tubular heat exchangers are ingeniously crafted devices designed for high-efficiency heat transfer between liquids and gases. They feature a robust tubular structure which maximizes surface area, thus enhancing the exchange rate of thermal energy. These devices are predominantly used in situations that require precise thermal control and maintenance, from energy production plants to food processing facilities.
The design of tubular heat exchangers is a testament to engineering prowess, tailored specifically to meet specific application needs with precision. Comprised typically of inner and outer tubes, they facilitate the transfer of heat between two fluids at different temperatures by means of conduction and convection. This design is not only efficient but incredibly flexible, allowing customization according to the industry-specific requirements. For instance, surface area modifications can be made to increase heat transfer efficiency through the addition of fins or by altering the diameter and length of the tubes.
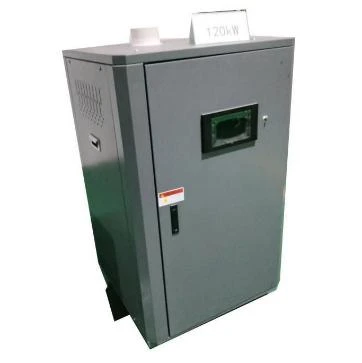
In practical applications, tubular heat exchangers have established themselves as indispensable assets. In the chemical industry, for example, they ensure that exothermic and endothermic processes maintain safe and efficient operational conditions. In the oil and gas sector, they are critical for refinery operations where they aid in the recovery of thermal energy, which significantly reduces operational costs. The food and beverage industry utilizes these exchangers to facilitate pasteurization and sterilization processes, ensuring product safety and quality.
The reliability of tubular heat exchangers underpins their authority in the field of thermal management. Their durability allows them to operate efficiently under high-pressure conditions and harsh environments, such as those found in petrochemical plants or aboard marine vessels. This robustness translates into reduced maintenance costs and longer operational life, lending credibility to their adoption across varied sectors.
tubular heat exchanger
Moreover, tubular heat exchangers are designed with materials that can withstand corrosive environments, such as stainless steel or titanium, enhancing their credibility and trustworthiness. This resistance to corrosion means they can reliably process a range of fluids without the risk of contamination or degradation, further highlighting their importance in sectors that demand high purity standards, such as pharmaceuticals or semiconductor manufacturing.
Among the notable benefits of tubular heat exchangers is their ability to achieve high levels of thermal efficiency with minimal fluid mixing, which is critical in maintaining product quality and consistency. The inherent design flexibility allows industries to tailor their heat exchange solutions, optimizing their systems for energy efficiency and cost-effectiveness. By minimizing energy wastage and maximizing heat recovery, these systems play a pivotal role in sustainable industrial operations, aligning with global initiatives towards reducing carbon footprints and promoting green energy practices.
An additional element reinforcing their authoritativeness is the ability to integrate advanced monitoring systems. Modern tubular heat exchangers can be equipped with sensors and predictive maintenance software that monitor performance parameters in real-time, allowing for proactive maintenance and reducing the likelihood of unscheduled downtimes.
In conclusion, tubular heat exchangers are a paradigm of engineering excellence, offering unparalleled efficiency and reliability in heat transfer applications. Their robust construction, material versatility, and adaptability to specific industry needs affirm their status as leaders in thermal management technologies. This authority is further bolstered by their capability to operate efficiently in complex, high-stakes environments and their alignment with sustainable operational practices. As industries continue to evolve, tubular heat exchangers will undoubtedly remain at the forefront, driving innovations in energy efficiency and thermal management solutions worldwide.