Exploring Water Glass Casting Suppliers A Comprehensive Guide
In the realm of manufacturing and metal casting, water glass casting, also known as sodium silicate or investment casting, stands as a pivotal process that merges precision with versatility. This technique, renowned for producing intricate and delicate parts with remarkable accuracy, has seen a surge in demand across various industries, including aerospace, automotive, and machinery. Consequently, identifying reliable water glass casting suppliers has become increasingly important for businesses seeking to harness the full potential of this technology. This article delves into understanding the essence of water glass casting, its advantages, and how to navigate the landscape of suppliers effectively.
**Understanding Water Glass Casting**
Water glass casting commences by creating a pattern, often made from wax or plastic, which represents the final product's shape. This pattern is then coated with a refractory material before being encased in a mold made primarily of a mixture of silica sand and sodium silicate, hence the term water glass. Upon heating, the wax melts out, leaving a cavity that perfectly mirrors the original pattern. Molten metal is poured into this cavity, allowed to solidify, and once cooled, the mold is broken away, revealing the cast part.
**Key Advantages of Water Glass Casting**
The allure of water glass casting lies in its ability to create complex geometries with exceptional surface finishes, all while maintaining tight tolerances. Some salient benefits include
1. **High Precision** Ideal for components requiring intricate details and tight dimensional control.
2. **Versatility of Materials** Supports a wide range of metals, including aluminum, steel, and various alloys.
3. **Cost-Effectiveness** Despite the intricate process, it can be more economical than other casting methods for small to medium production runs.
4. **Reduced Need for Secondary Operations** Parts often require minimal machining post-casting due to the high accuracy achieved.
**Identifying Quality Water Glass Casting Suppliers**
Navigating the market to find the right water glass casting supplier involves a meticulous approach centered around several key factors
1. **Experience and Expertise** Look for suppliers with a proven track record in water glass casting, especially those specializing in your industry **Experience and Expertise** Look for suppliers with a proven track record in water glass casting, especially those specializing in your industry
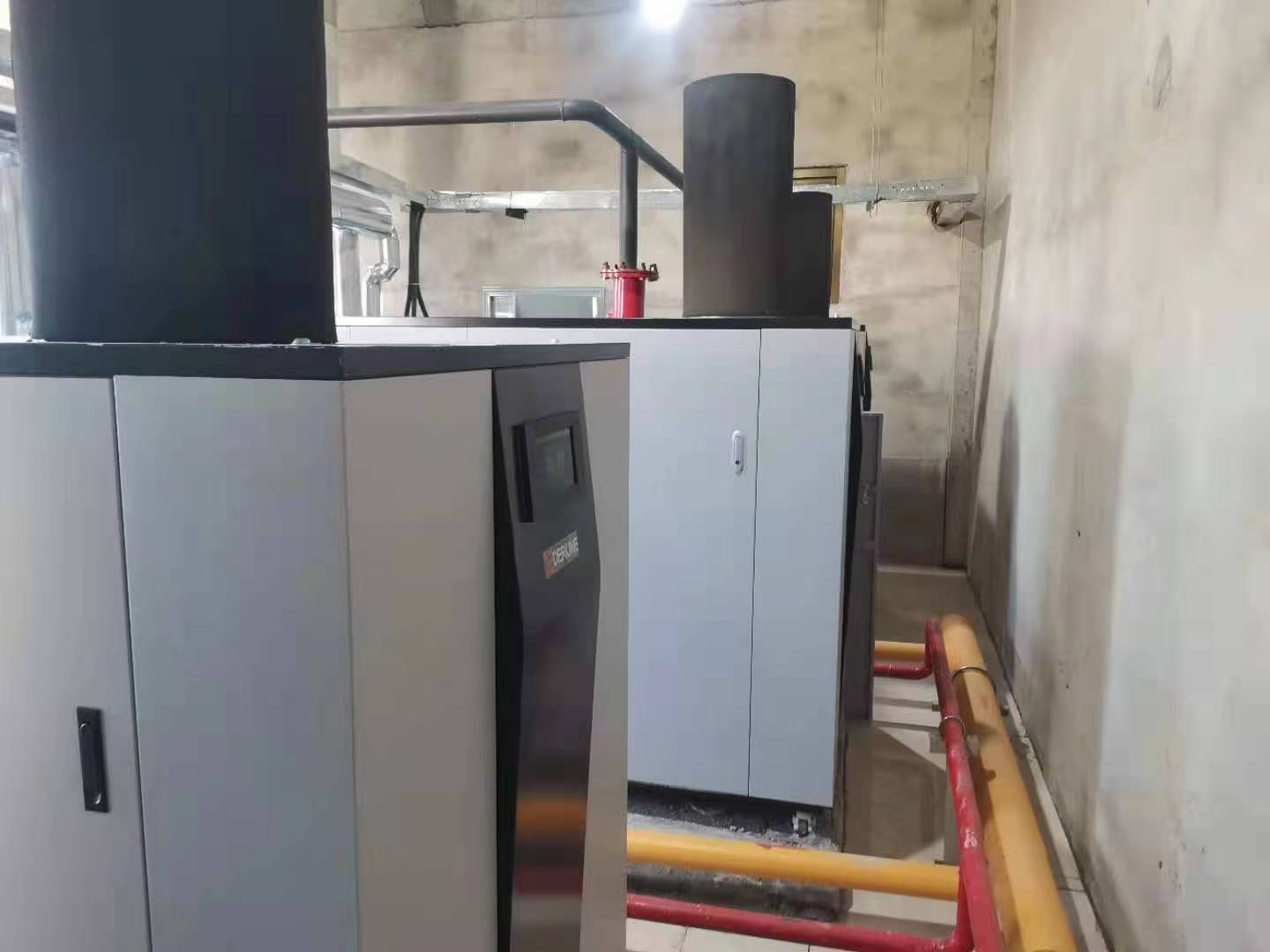
**Experience and Expertise** Look for suppliers with a proven track record in water glass casting, especially those specializing in your industry **Experience and Expertise** Look for suppliers with a proven track record in water glass casting, especially those specializing in your industry
water glass casting suppliers. Their experience can translate into better process control and problem-solving capabilities.
2. **Quality Assurance** Ensure the supplier adheres to international quality standards such as ISO 9001. Request samples and inspect their quality control measures to guarantee consistency and reliability.
3. **Technology and Infrastructure** Advanced technology, including computer-aided design (CAD) and 3D printing for pattern making, speeds up prototyping and enhances accuracy. Assess the supplier's technological capabilities to understand their potential to deliver on complex projects.
4. **Customization and Flexibility** A good supplier should be able to accommodate customization requests and offer flexible production volumes, from prototypes to mass production.
5. **Communication and Service** Effective communication is paramount. Suppliers who provide dedicated account management, prompt responses, and clear project timelines foster a smoother collaboration process.
6. **Environmental Responsibility** With growing emphasis on sustainability, consider suppliers who implement eco-friendly practices in their operations, such as recycling waste materials and using energy-efficient processes.
**Conclusion**
In the quest for excellence in water glass casting, partnering with the right supplier is tantamount to success. By meticulously evaluating suppliers based on their expertise, quality assurance, technological prowess, flexibility, communication skills, and commitment to environmental stewardship, businesses can unlock the full potential of this casting method. As the demand for intricate and precise metal components continues to rise, establishing a robust supply chain with a trusted water glass casting supplier becomes a strategic imperative for companies seeking to stay competitive in today's dynamic marketplace.