Enhancing Energy Efficiency with Water-to-Water Shell and Tube Heat Exchangers
In the pursuit of energy efficiency, water-to-water shell and tube heat exchangers have emerged as a crucial technology within industrial processes. These devices facilitate the transfer of thermal energy between two fluids, separated by a solid wall, without allowing the fluids to mix. The design and application of such heat exchangers are pivotal in managing temperature control, which is essential for numerous industrial applications.
The operational principle of water-to-water shell and tube heat exchangers is rooted in the fundamental laws of thermodynamics. They consist of multiple tubes that are mounted inside a hollow shell. One water stream flows through the tubes while the other stream surrounds them within the shell. This configuration optimizes the surface area available for heat transfer, ensuring maximum efficiency.
One notable advantage of using water as the medium in these systems is its high specific heat capacity, meaning it can absorb or release significant amounts of heat with minimal temperature changes. This property makes water an ideal choice for processes requiring precise temperature management.
The effectiveness of a water-to-water shell and tube heat exchanger is determined by several factors, including the design of the tubes, the materials used, and the flow rates of the water streams. Material selection is particularly important since it must withstand corrosion from water and the temperatures involved Material selection is particularly important since it must withstand corrosion from water and the temperatures involved
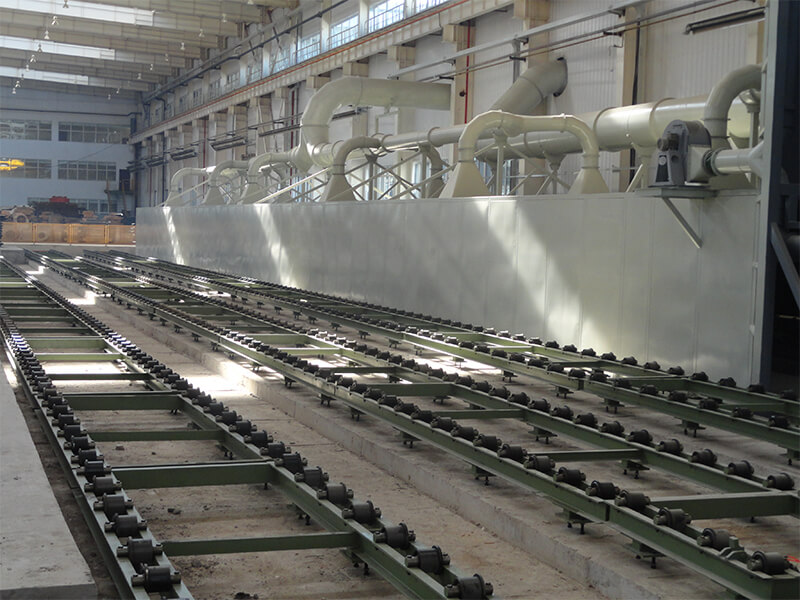
Material selection is particularly important since it must withstand corrosion from water and the temperatures involved Material selection is particularly important since it must withstand corrosion from water and the temperatures involved
water to water shell and tube heat exchanger. Common materials include stainless steel, titanium, and copper alloys, each with their unique benefits and drawbacks.
In terms of maintenance, water-to-water shell and tube heat exchangers generally require less attention compared to other types due to the relatively clean nature of water as a heat transfer fluid. However, regular inspections are necessary to monitor for scaling, biofouling, or leaks that could impair performance.
The implementation of water-to-water shell and tube heat exchangers in industries such as HVAC (Heating, Ventilation, and Air Conditioning), refrigeration, and process heating has led to substantial energy savings. By reclaiming waste heat from one process and utilizing it to preheat water for another, these systems not only conserve energy but also reduce operating costs and environmental impact.
In conclusion, water-to-water shell and tube heat exchangers represent a vital component in the drive towards more efficient and sustainable industrial practices. Their ability to effectively manage thermal energy transfer plays an integral role in reducing energy consumption and optimizing production processes. As technology continues to advance, the design and application of these heat exchangers will undoubtedly evolve, further enhancing their contribution to energy conservation efforts worldwide.