Sodium silicate sand casting is a time-tested method that's gaining renewed interest in the modern manufacturing landscape. It combines the benefits of traditional foundry processes with the advancements of modern material science, creating a niche that's ripe for innovative applications and enhanced product outcomes.
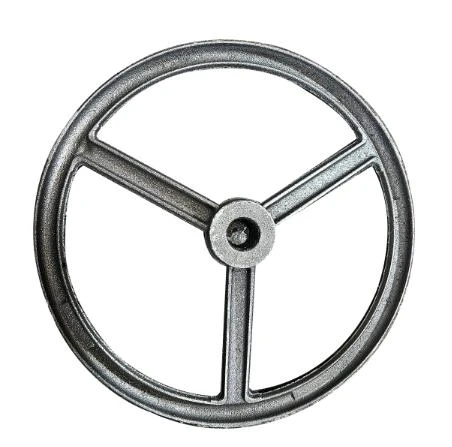
In essence, sodium silicate sand casting involves creating molds by binding sand with a sodium silicate solution. Upon exposure to CO2 gas, the binder hardens, forming a solid mold that can withstand the pouring of molten metal. This methodology is cherished for its precision and ability to produce complex geometric components, making it indispensable in industries such as aerospace, automotive, and heavy machinery.
From an expertise perspective, the primary advantage lies in the environmental and safety benefits it offers over other casting methods. Unlike resin-based binders, sodium silicate does not emit significant volatile organic compounds (VOCs) during the process, ensuring a safer workspace. Furthermore, its inorganic nature translates to ease of reclamation and reuse of the sand, aligning with sustainable manufacturing practices.
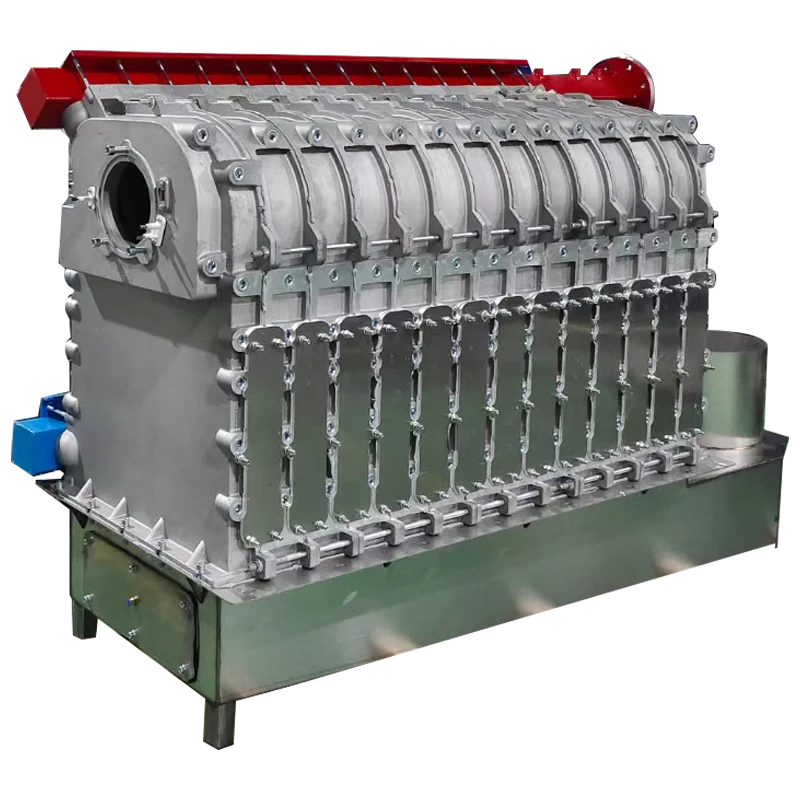
Real-world experience highlights the flexibility and efficiency sodium silicate sand casting provides practitioners. In high-demand production environments, this method expedites mold creation due to the rapid solidification upon CO2 application. This speed, combined with the capacity to produce highly detailed casts, makes it a go-to for prototype development and time-sensitive projects.
Expertise in this domain also concerns the careful selection of process parameters — the sand grain size, sodium silicate concentration, and CO2 exposure timing critically influence the mold quality. Poorly calibrated processes can lead to defects such as surface roughness or incomplete casts. Thus, understanding these nuances ensures optimal production outcomes, emphasizing precision engineering.
Authority within sodium silicate sand casting is often seen in the form of advanced systems developed by industry leaders who engineer solutions that enhance the process. These systems use state-of-the-art equipment to automate the mixing and handling of sand and binding agents, leveraging data analytics for quality control and efficiency. Such innovation not only boosts productivity but also ensures consistent product quality, further solidifying the method's standing in manufacturing.
sodium slicate sand casting
Trustworthiness, the final pillar, is built on a foundation of rigorous quality assurance protocols. Certified supply chains ensure that raw materials like sodium silicate and the sand meet stringent standards, reducing variability in the end products. Additionally, ongoing research and development continue to refine casting techniques, promising future enhancements in durability, cost-effectiveness, and environmental impact.
For those involved in producing safety-critical components, sodium silicate sand casting offers unparalleled reliability. It enables the creation of casts that meet precise performance criteria, essential for industries where failure is not an option. Users thereby gain confidence in their products' structural integrity and longevity, vital attributes in sectors like transportation and infrastructure.
A compelling case study can be observed in the renewable energy sector, where wind turbine components demand exceptional strength and precision. Utilizing sodium silicate sand casting, manufacturers can efficiently produce robust hubs and blades, ensuring that these colossal structures withstand immense operational stresses. As a result, this environmentally friendly casting method is pivotal in advancing cleaner energy solutions.
Innovation does not rest within any field,
and sodium silicate sand casting is no exception. Emerging technologies, such as AI-driven process control and additive manufacturing, are merging with traditional casting techniques to further enhance design capabilities and operational efficiency. These developments not only promise to improve the competitiveness of sodium silicate sand casting but also signal a promising future for custom manufacturing applications.
In conclusion, sodium silicate sand casting represents a harmonious blend of historical techniques and cutting-edge innovation. Its growing relevance is fueled by its eco-friendly nature, adaptability, and the rigorous quality that industries demand today. As manufacturing moves towards a more sustainable and technologically integrated future, this casting method stands out as a robust, trusted choice for producing high-performance components that meet the challenges of tomorrow.