Gravity casting, a pivotal technique in the manufacturing industry, stands out for its ability to produce high-quality, durable metal parts. This method, involving the pouring of molten metal into a mold under the force of gravity, boasts a rich history and profound applicability in today's industrial sector. Its uniqueness and effectiveness in crafting diverse components make it a subject worthy of exploration.
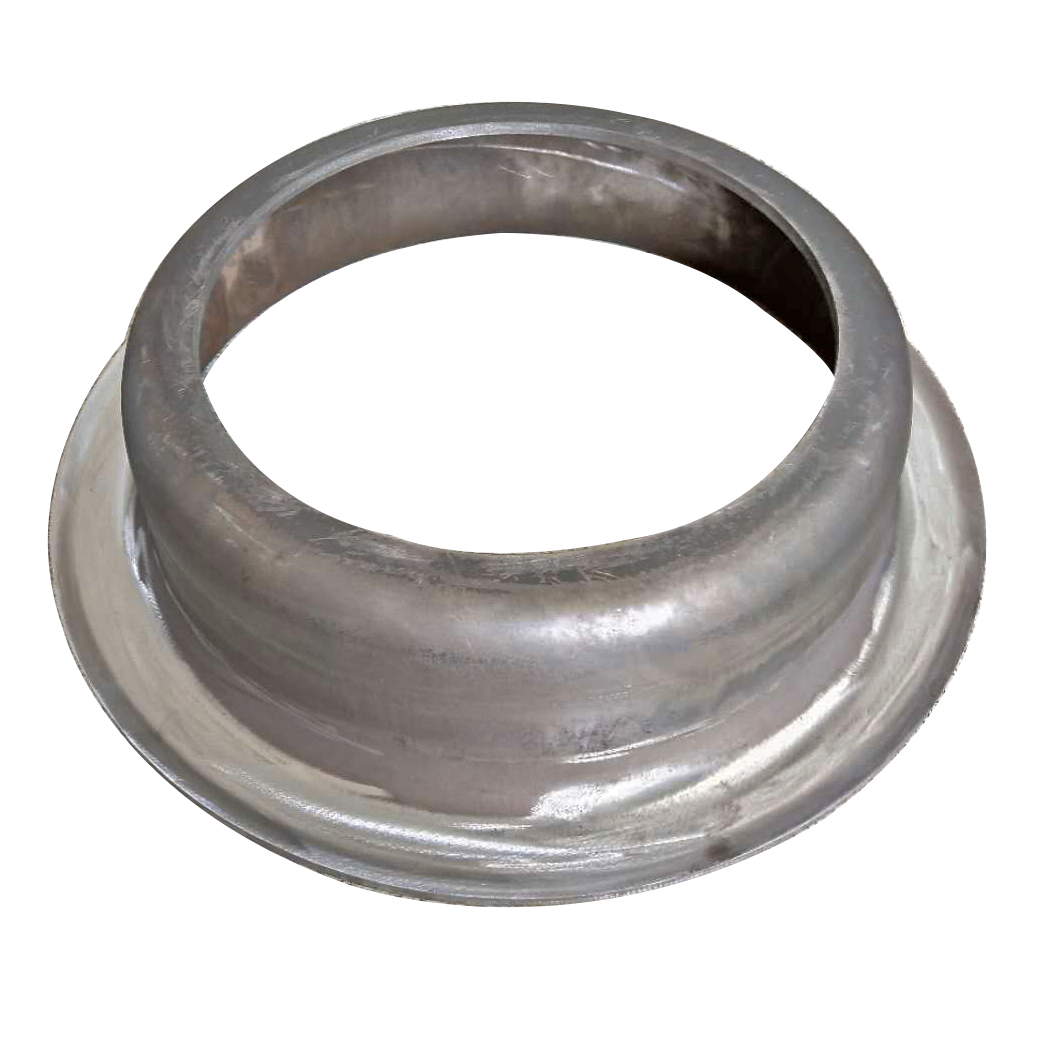
Historically, gravity casting has been a cornerstone of metalworking, tracing its origins back to ancient civilizations that utilized this technique for creating utilitarian and ornamental items. Over time, advances in technology have refined gravity casting into a precise method capable of meeting modern demands. From the production of automotive components to intricate parts for aerospace and defense, this casting method continues to demonstrate its versatility and reliability.
The process of gravity casting begins with the creation of a mold, typically made from materials such as sand, metal, or ceramic, capable of withstanding extreme temperatures. Once the mold is prepared, molten metal is carefully poured into it, relying solely on the gravitational force to distribute the material. This aspect of the process underscores the importance of mold design; the shape, size, and intricacy of the mold govern the final product's quality and consistency.
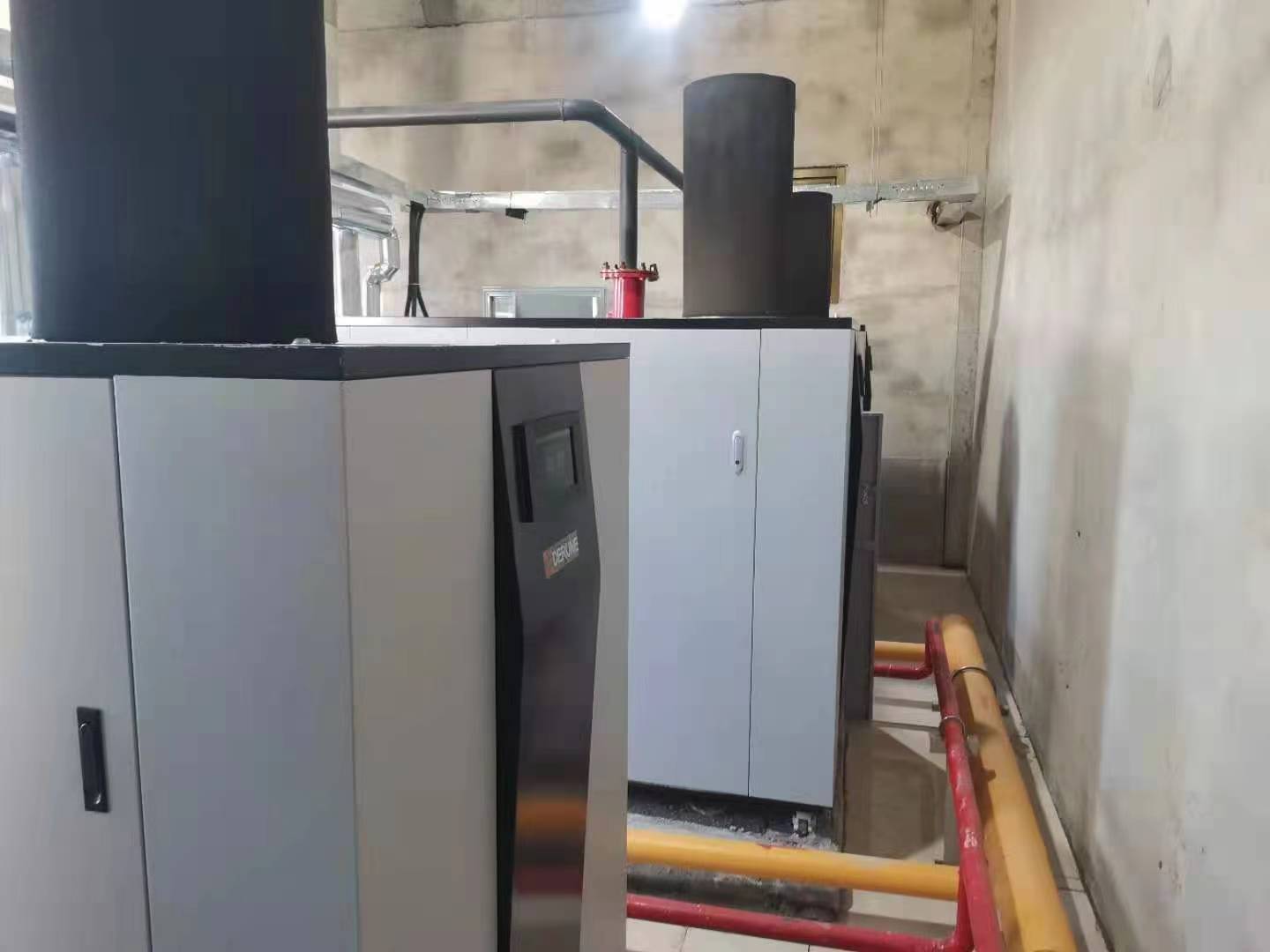
An advantage of gravity casting over other casting methods lies in its simplicity and cost-effectiveness, particularly for medium to large production runs. Unlike pressure casting techniques, gravity casting does not require expensive machinery or high-pressure equipment, making it accessible to a wide array of manufacturers. Furthermore, this method generates fewer defects and results in a smoother surface finish, reducing the need for extensive post-casting machining. This efficiency not only minimizes waste but also enhances production throughput—important factors for companies aiming to optimize manufacturing operations.
gravity casting
Moreover, gravity casting supports a broad range of metals and alloys, including aluminum, bronze, and magnesium, each offering distinct benefits. Aluminum, for instance, is known for its lightweight properties and corrosion resistance, making it ideal for automotive and aerospace applications. Bronze provides excellent wear resistance, often used in marine and heavy machinery industries. By selecting the appropriate material, manufacturers can tailor the mechanical and physical properties of the final component to specific application requirements.
Quality control remains a critical aspect of the gravity casting process. Through advanced inspection techniques, such as X-ray analysis and ultrasonic testing, manufacturers can identify and rectify potential flaws within the cast components. This emphasis on quality assurance not only affirms the reliability and performance of the gravity-cast parts but also fortifies the trust between manufacturers and clients. Enhanced transparency and traceability in production processes further enhance this trust, positioning gravity casting as a trustworthy method in the eyes of discerning consumers.
The future of gravity casting is promising, with ongoing research and development focused on improving its capabilities. Innovations in mold materials and casting techniques continue to emerge, enabling finer detail and complexity in gravity-cast components. Furthermore, the integration of computer-aided design and simulation tools allows manufacturers to optimize mold designs and casting parameters, reducing production cycles and opening new possibilities for customized and large-scale production scenarios.
For businesses seeking a manufacturing technique that balances efficiency, quality, and adaptability, gravity casting presents a compelling option. Its ability to deliver robust, highly detailed, and performance-oriented components makes it a valuable asset in a wide spectrum of industries. By choosing gravity casting, manufacturers not only benefit from centuries of expertise but also position themselves at the forefront of modern manufacturing innovation, trusted by a global clientele.