When it comes to optimizing the efficiency of industrial processes, size does matter, especially within the realm of heat exchangers. A crucial component in various sectors, heat exchangers facilitate the transfer of heat between two or more fluids, impacting everything from energy consumption to production efficiency. In this comprehensive guide, we delve into the essential aspects of sizing heat exchangers, drawing from real-world experience, technical expertise, authoritative insights, and trustworthy methodologies, to offer you an unmatched perspective on optimizing these systems for superior performance.
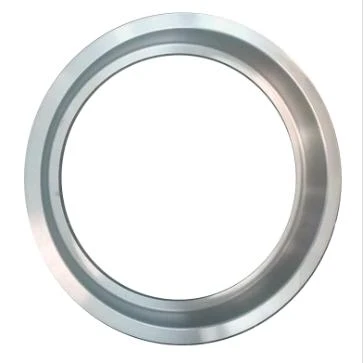
Choosing the right size for a heat exchanger is not merely an exercise in mathematical calculation; it is a nuanced process involving keen analysis of operational requirements and specific industry applications. In our extensive experience, the key lies in balancing capacity and efficiency, bearing in mind the unique demands of your facility. Over-sized units can lead to unnecessary energy expenditures and increased operational costs, while under-sized systems may fail to meet production needs, resulting in operational downtime and loss of efficiency.
From an expertise standpoint, understanding the principles of thermodynamics and fluid mechanics is essential. For instance, the heat transfer area directly influences a heat exchanger’s capacity, while the choice of materials impacts thermal conductivity and durability. Stainless steel and titanium are often preferred for their excellent thermal properties and resistance to corrosion, an important consideration in industries like chemical processing or marine applications where harsh conditions prevail.
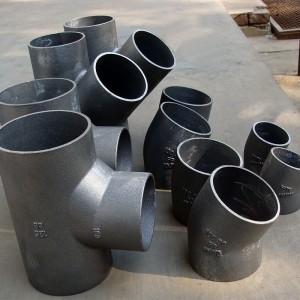
Authority in sizing heat exchangers is established through adherence to recognized standards and industry best practices. Organizations like the Tubular Exchanger Manufacturers Association (TEMA) and the American Society of Mechanical Engineers (ASME) provide detailed guidelines on design and performance expectations. Compliance with these standards ensures not only optimal performance but also safety and reliability, reducing the risk of costly setbacks and establishing client confidence in your systems.
Trustworthiness in the heat exchanger domain stems from transparency and data-driven decision-making. Utilizing sophisticated software tools and predictive models allows for precise calculations related to temperature gradients, pressure drops, and flow rates. Furthermore, field validation and regular maintenance checks serve as vital processes to confirm that the heat exchanger operates within its designed parameters, ensuring long-term effectiveness and sustainability.
Innovation in heat exchanger technology continues to evolve, offering new opportunities for efficiency gains and reduced environmental impact. Compact microchannel heat exchangers, for example, have introduced groundbreaking improvements in thermal performance and material consumption. These smaller, more environmentally friendly models align well with current trends towards sustainable and energy-efficient industrial practices.
To distill our extensive knowledge into actionable advice, consider these key steps for optimizing heat exchanger size
size heat exchanger
1. Define Operational Requirements Carefully assess the heat load requirements specific to your application, considering variables such as fluid type, temperature differentials, and flow rates.
2. Select Suitable Materials Prioritize materials based on heat transfer effectiveness, chemical compatibility, and potential for corrosion under your specific operating conditions.
3. Adhere to Standardized Guidelines Align your design with industry-recognized standards, ensuring compliance for safety, efficiency, and reliability.
4. Leverage Technological Advances Incorporate innovative designs and materials, such as compact heat exchangers, to enhance thermal performance and reduce environmental impact.
5. Maintain Regular Check-Ups Implement routine inspections and performance assessments to catch potential issues early and ensure consistent operational efficiency.
Ultimately,
the correct sizing of a heat exchanger is a determinant of a facility’s success. By prioritizing efficiency, meeting recognized standards, and embracing innovation, you can ensure that your heat exchanger functions at optimal capacity, minimizing costs and maximizing productivity. Drawing from cutting-edge technology and proven methodologies, your journey towards enhanced performance begins with informed decision-making and strategic planning in heat exchanger sizing.