In the ever-evolving landscape of industrial applications, heat exchangers are pivotal devices ensuring thermal regulation across various industries. Among the key players, BAC heat exchangers have emerged as a hallmark of innovation and efficiency, marrying advanced technology with practical application. These devices are not just components in a system; they are engineered solutions integral to operations involving heating, cooling, and energy conservation.
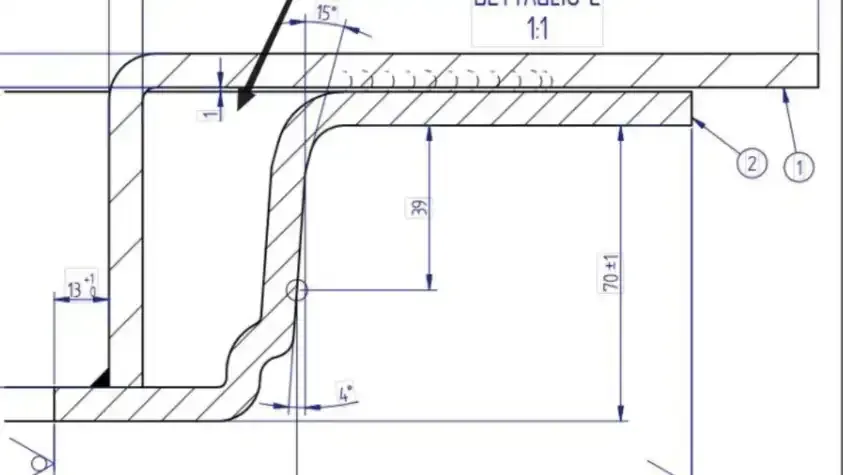
The sophistication of BAC heat exchangers is rooted in their design and operational principles that stem from a blend of engineering expertise and real-world testing. These exchangers are specifically tailored to meet the demands of industries such as HVAC, chemical processing, power generation, and manufacturing, where maintaining precise thermal conditions is critical. By optimizing heat transfer between different mediums – whether liquid-to-liquid, air-to-liquid, or gas-to-liquid – BAC heat exchangers facilitate superior heat dissipation, crucial for maintaining the efficiency of machinery and processes.
Expertise in the field has long recognized the need for reliability and longevity in heat exchanger technology. BAC heat exchangers are developed with a focus on durability, leveraging materials like stainless steel and copper alloys known for their resistance to corrosion and thermal expansion. This choice of materials reflects a deep understanding of the environments these exchangers operate in, often exposed to extreme conditions of temperature and pressure, ensuring long-term performance without frequent maintenance.
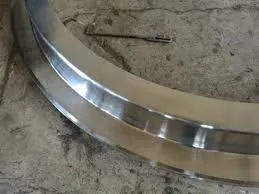
A testament to the authoritativeness of BAC heat exchangers is their adherence to international standards and certifications. Typically, these exchangers comply with ASME, CE, and ISO, among others, reassuring industries of their safety and quality standards. Such certification processes are not merely a formality; they embody thorough testing and validation of the technological aspects, confirming that each exchanger is up to the task in demanding industrial settings.
bac heat exchangers
The sophistication of BAC heat exchangers goes beyond materials and design. These devices incorporate cutting-edge thermal technologies to maximize efficiency, often employing counterflow designs, finned tubing, and advanced plate configurations. By enhancing the surface area for heat transfer and optimizing flow paths, BAC exchangers achieve a thermal performance that sets industry benchmarks. This expertise is critical for companies aiming to minimize energy costs while maximizing operational output.
Trustworthiness in high-performance environments often boils down to experience. BAC heat exchangers are the result of decades-long R&D initiatives, field trials, and user feedback loop integration. The benefit of this experience is reflected in heat exchangers that are not only high performance but also customizable to specific application needs. For instance, industries facing unique challenges such as biofouling in marine settings or scaling in water treatment can rely on BAC's adaptable designs to address these effectively.
Furthermore, the transition towards greener technologies is seamlessly incorporated into the design of BAC heat exchangers. They often feature designs that reduce environmental impact by improving energy efficiency and utilizing eco-friendly refrigerants. In industries pressured by both economic factors and environmental regulations, BAC emerges as a leader in providing sustainable solutions without compromising on performance.
In conclusion, the hallmark of BAC heat exchangers lies in their unmatched balance of expertise, authority, and trust. They are not merely parts of larger systems but are pivotal components designed to alleviate the complexities of thermal management in modern industries. For businesses looking to enhance their thermal efficiency while ensuring reliability and sustainability, BAC heat exchangers present the ideal choice, supported by a legacy of innovation and a commitment to quality.