The construction industry continually evolves with innovations that deliver both efficiency and durability.
One such advancement is the dry-cast reinforced concrete pipe (RCP) bottom ring, a critical component in infrastructure projects. This article unravels the intricacies of dry-cast methodology, focusing on its application in producing bottom rings for reinforced concrete pipes.
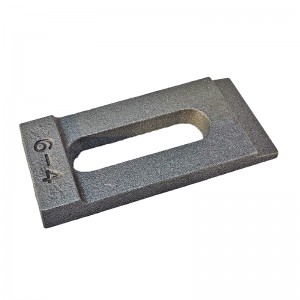
Dry-cast concrete technology is renowned for its efficiency in producing high-density, durable concrete products ideal for sewer and drainage systems. Unlike traditional wet-cast methods, dry-casting involves a mixture with a low water-to-cement ratio, similar to the consistency of the soil. This method benefits from rapid curing times, allowing for swift manufacturing cycles essential in high-demand environments.
The bottom ring of a concrete pipe is a crucial element, acting as the foundational support and the primary point of contact with the ground. The introduction of dry-cast technology in manufacturing these bottom rings ensures a product that withstands significant environmental and structural stresses. This technology significantly reduces voids and increases the overall strength due to the compacted nature of the mix, thus providing superior load-bearing capabilities and enhancing the lifespan of the construction.
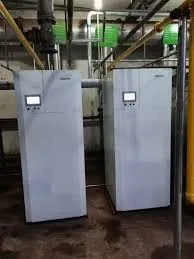
A standout feature of the dry-cast method is its contribution to sustainability within the construction industry. By using less water and cutting down on curing time, it reduces the carbon footprint of production facilities. The adoption of eco-friendly practices not only meets regulatory standards but also positions companies as leaders in sustainable construction solutions, appealing to environmentally-conscious clientele.
The industry expertise required to implement dry-cast technology effectively cannot be understated. Engineers and production managers must thoroughly understand the mix design, compaction methods, and quality control processes. Proper training and equipment are crucial to ensure consistency in product quality. Precision in these areas assures clients of the dependability and safety of the structures built using dry-cast RCP bottom rings.
dry-cast reinforec concrete pipe bottom ring
For firms contemplating this technology, collaboration with industry experts and participation in training workshops are invaluable. Such initiatives boost a company’s authority in the field, assuring clients of their commitment to cutting-edge technologies and superior service delivery. This assurance is especially significant when constructing drainage and sewage systems in urban environments, where failure could result in catastrophic infrastructural consequences.
In a landscape where trust is paramount, dry-cast reinforced concrete pipe bottom rings offer reliability backed by technological advancement. This technology has been subject to extensive testing and has consistently exceeded industry standards, making it a trusted choice for engineers and city planners worldwide.
Companies investing in dry-cast technology benefit from enhanced production timelines and reduced product failure rates, gaining a competitive edge in the market. Furthermore, their commitment to innovative, environmentally-friendly methods secures their reputation as leaders in quality and sustainability.
The narrative surrounding dry-cast reinforced concrete pipe bottom rings is not just about technological advancement; it is about driving progress in building practices that blend durability, efficiency, and environmental consciousness. As infrastructure needs evolve, the demand for robust, reliable construction solutions will only see an upward trend. Embracing such innovations ensures readiness for future challenges and opportunities in the urban development sector.
In conclusion, dry-cast technology in producing reinforced concrete pipe bottom rings signifies a shift towards more sustainable and durable construction methods. Its integration into current building practices not only enhances the strength and reliability of vital infrastructure but also demonstrates a commitment to innovation and sustainability, marking a new era in the concrete products industry.