Investment castings, also known as precision castings or lost-wax castings, have become a critical component in various industries due to their unparalleled ability to produce complex geometries with tight tolerances and excellent surface finish. This manufacturing process, which traces its origins to ancient civilizations, continues to evolve, providing industries such as aerospace, automotive, and medical with parts that meet stringent specifications and performance standards.
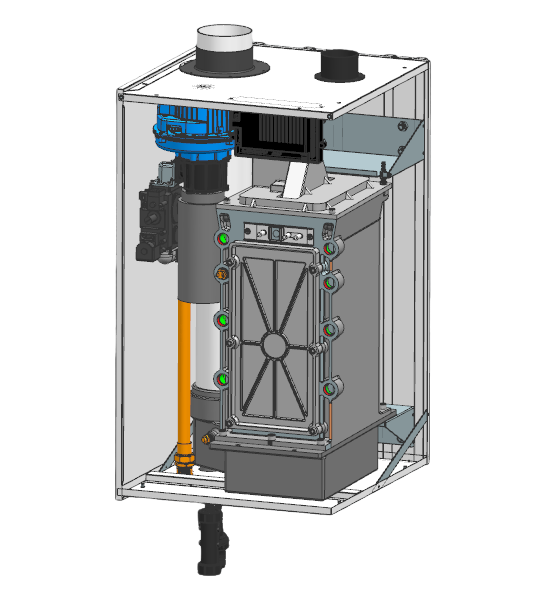
One of the primary advantages of investment casting lies in its ability to produce parts with intricate details and dimensional accuracy. This process allows the production of components that would be nearly impossible, or prohibitively expensive, to create through conventional machining or other casting methods. The preciseness of investment castings reduces the need for machining, leading to cost savings and shortened production timelines.
Industries across the spectrum value investment castings for their versatile material applications. From stainless steel and aluminum to more exotic alloys, the investment casting process supports an extensive range of materials, granting engineers the flexibility to choose the most appropriate material for their specific application. For instance, in the aerospace industry, lightweight yet strong materials are paramount. Investment casting effectively produces parts from titanium and nickel-based superalloys, which are crucial in manufacturing turbine blades and structural components that endure extreme conditions and high stress.
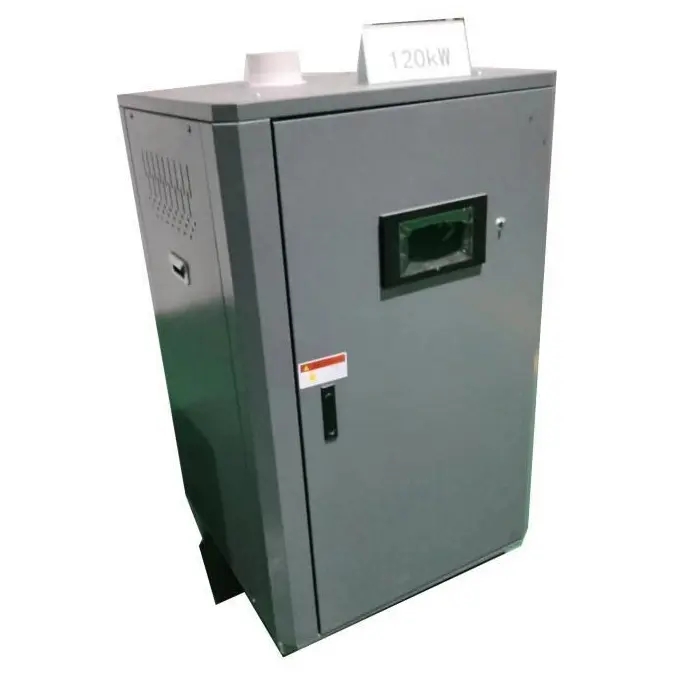
The expertise required in investment casting is immense, demanding a thorough understanding of material science, engineering principles, and foundry technology. Professionals in the field are adept at controlling the numerous variables in the casting process, such as wax pattern generation, mold making, and the final casting and finishing operations. Such expertise ensures that every casting not only meets the specified mechanical properties and dimensions but also adheres to the meticulous quality standards expected in high-stakes applications.
investment castings
Trust is an indispensable element when selecting a supplier for investment casting. Manufacturers with established reputations provide assurance through certifications and quality checks, such as ISO 9001 or AS9100, which certify adherence to international standards in production and quality management. These certifications demonstrate a commitment to maintaining quality and reliability at every stage of the casting process, from initial design consultations to final part inspection.
Real-world experience plays a crucial role in the investment casting realm. Manufacturers leverage decades of practice and continuous learning to refine their processes, often collaborating closely with clients to achieve customized solutions. Case studies frequently highlight how investment casting providers have innovated to meet unique challenges presented by clients, such as reducing component weight, enhancing durability, or improving heat resistance, thereby proving their commitment and capability to adapt and innovate.
The future of investment casting is promising, especially with emerging technologies like 3D printing and automated casting systems poised to integrate seamlessly with traditional methods. These advancements offer the potential to reduce lead times further, improve consistency, and allow for even more complex geometries to be explored. By combining the timeless principles of investment casting with state-of-the-art technology, manufacturers can continue to push the boundaries of what is possible.
In conclusion, investment casting stands as a testament to precision and adaptability in the manufacturing sector. Its ability to produce detailed, high-performance parts consistently makes it a valuable asset across numerous industries. By choosing experienced and reputable manufacturers, businesses can leverage this expert craftsmanship to achieve superior product performance and inherently trust in the quality of each component produced.