Lost wax casting, a time-honored technique that dates back thousands of years, is cherished for its precision and versatility in creating intricate products, particularly in the jewelry and fine arts industries. Yet, there's an often-overlooked aspect of this process that could significantly enhance the efficiency and environmental friendliness of manufacturing lost wax wasting. Understanding and optimizing this facet can revolutionize how businesses approach production, making them more sustainable and cost-effective.
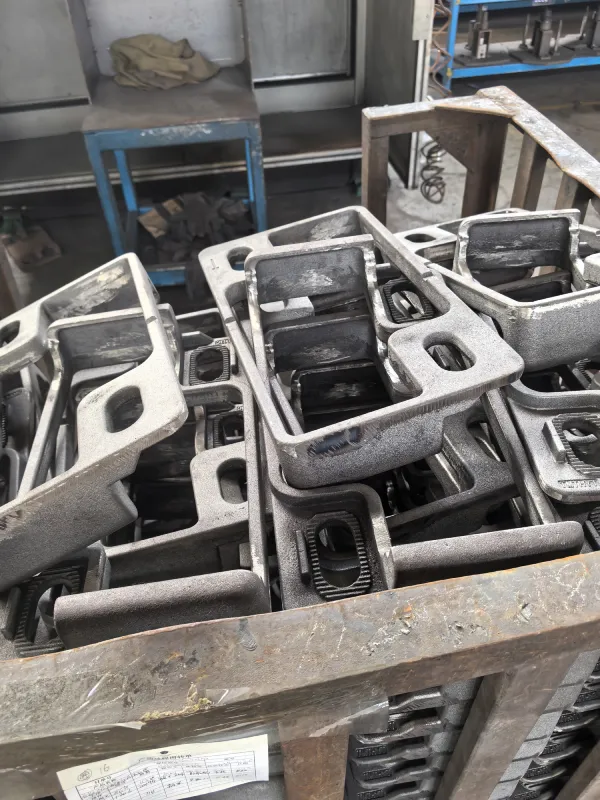
Lost wax wasting involves the strategic utilization of resources throughout the casting process. Traditionally, this process starts with sculpting a detailed model in wax, which is then encased in a heat-resistant material to form a mold. Once the mold solidifies, the wax model is melted and lost, leaving behind a cavity that is subsequently filled with molten metal to create the final product. The critical issue at hand is what happens to the wax in this process; the efficiency with which companies manage this phase can significantly influence both their bottom line and environmental impact.
An innovative approach to mitigating lost wax wasting involves focusing on wax recovery and recycling. Advanced systems now allow for the recovery of a significant percentage of the wax, converting what was once a significant source of waste into a reusable resource. By investing in wax recycling technologies, companies can reduce material costs, create less environmental waste, and even improve the quality of the end products. This not only showcases a company's commitment to sustainability but also positions it as an industry leader in environmental responsibility.
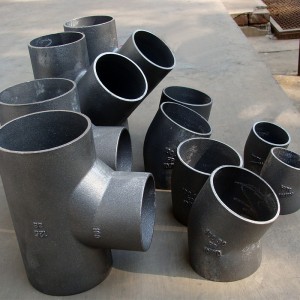
In terms of expertise, it is essential to understand the specific properties and behavior of different types of wax used in the casting process. Each type of wax responds differently to heating and cooling cycles, which affects both the quality of the mold and the feasibility of wax recovery. Professionals with an advanced understanding of materials science can tailor wax compositions to maximize yield and recyclability, thus fine-tuning the process to their specific production needs.
lost wax wasting
Authoritativeness in addressing lost wax wasting can be significantly boosted by adopting industry standards and affiliations with environmental organizations. Achieving certifications for sustainable practices can dramatically enhance a brand's reputation. Collaborating with organizations focused on sustainable manufacturing can provide additional resources and support, further establishing a company as a leader in eco-conscious production methodologies.
Trustworthiness is built through transparency and consistency in sustainable practices. Companies should not only implement but also actively promote their waste reduction strategies and results. This can be achieved by publishing annual sustainability reports, engaging in social responsibility initiatives, and actively educating stakeholders and the public about their green practices and achievements in minimizing lost wax waste. Openly sharing such information can foster a loyal customer base and attract clients increasingly concerned with corporate sustainability.
Harnessing the potential of addressing lost wax wasting is not only a step towards better resource management but a strategic move that aligns with global sustainability trends. As consumer awareness and legislative pressures mount, shifting towards a circular economy model that includes waste reduction and recycling becomes not just beneficial but necessary. Companies that act now to address lost wax wasting will find themselves at the forefront of the industry, reaping the benefits both economically and reputationally. Embracing this evolution signifies a commitment to excellence and responsibility, ensuring longevity and relevance in an ever-changing market landscape.