LP boilers, or low-pressure boilers, serve an essential role across various industries by providing an efficient source of heat and energy. They operate at lower pressures compared to high-pressure counterparts, making them suitable for applications where intense heat is not necessary. As an expert in the field, understanding the nuanced applications, advantages, and maintenance of LP boilers can significantly enhance operational efficiency and safety in utilizing these machines.
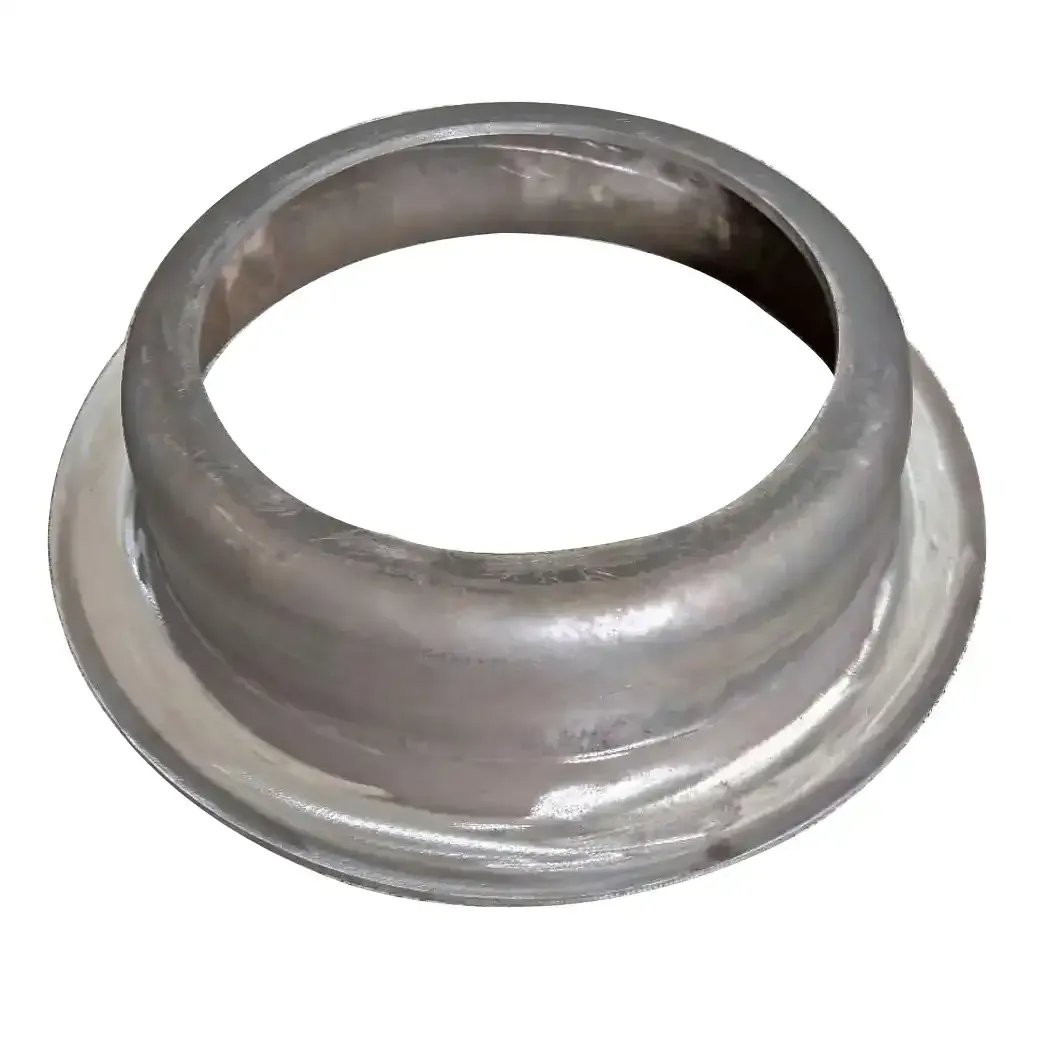
One of the standout qualities of LP boilers is their versatility. They are commonly employed in commercial settings, such as hospitals, schools, and office buildings, where they meet substantial but not excessive heating demands. Their adaptability is crucial in these scenarios, as they can seamlessly integrate into existing systems without requiring extensive modifications. Furthermore, industries like food processing and textiles benefit from LP boilers for processes that require gentle, consistent steam.
A critical aspect of LP boilers that underscores their reliability is their design simplicity. This simplicity translates into fewer components and connections that could potentially fail, thus reducing downtime and maintenance costs. Their straightforward design also facilitates easier access for cleaning and repairs, maintaining long-term efficiency and safety. The robustness of LP boilers significantly minimizes the risk of breakdowns, contributing to their dependability.
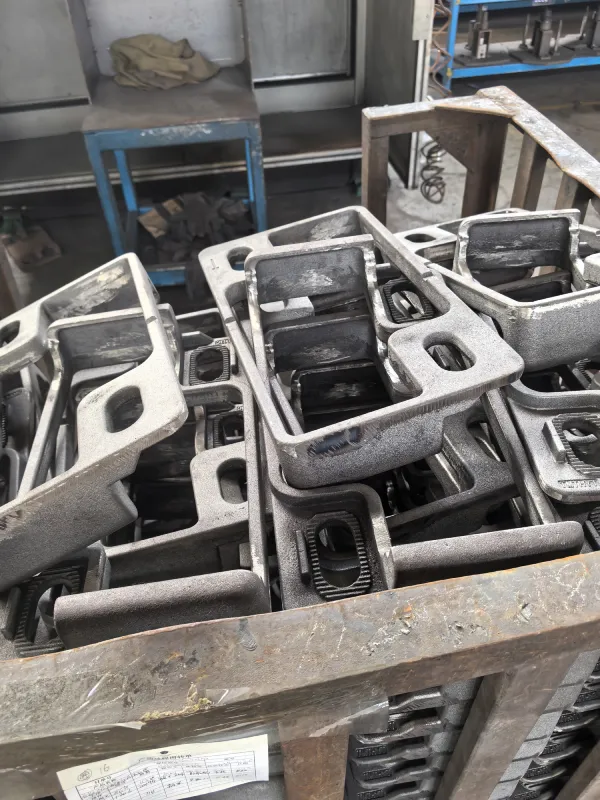
Efficiency is another hallmark of LP boilers. By operating at lower pressures, these boilers often entail reduced fuel consumption, lessening operational costs. In an era where energy efficiency and sustainability are at the forefront of industrial priorities, LP boilers meet these demands. Their energy efficiency not only translates to economic savings but also aligns with environmental regulations that many organizations aim to meet or exceed.
Safety is paramount when implementing any heating system. LP boilers, with their low pressure, inherently pose a lower risk compared to high-pressure systems. This intrinsic safety feature makes them particularly appealing for applications where safety is a high concern or where personnel may not have specialized training for handling high-pressure systems. Regular maintenance and inspections further enhance the safety of these systems, ensuring they operate within their designed parameters.
lp boilers
To maximize the benefits offered by LP boilers, regular maintenance is indispensable. Establishing a routine maintenance schedule can preemptively address issues such as scale build-up, corrosion, and mechanical wear. Conducting regular water quality checks and ensuring proper chemical treatment can prevent scale and corrosion, enhancing the lifespan and efficiency of the boiler. Additionally, inspecting safety valves and controls is crucial to maintain operational integrity.
When selecting an LP boiler, considering the total cost of ownership (TCO) is essential. This includes not just the initial purchase price but also installation costs, operational costs, maintenance expenses, and the expected lifespan of the unit. Modern LP boilers come equipped with advanced control systems that provide real-time performance data, enabling more efficient operations and proactive maintenance approaches.
Moreover, the digital integration of LP boilers into broader facility management systems can streamline operations further. Smart technology allows for remote monitoring and control, optimizing the performance and energy usage with minimal human intervention. Immediate alerts can be set up for system deviations, enhancing responsive maintenance and reducing the likelihood of unexpected downtime.
In conclusion, LP boilers present a reliable, efficient, and safe heating solution suitable for numerous applications. Their adaptability, combined with modern advancements in energy management and maintenance, makes them a viable choice for organizations looking to improve operational efficiency while adhering to safety and environmental standards. Understanding their operation, management, and integration into existing systems is key to leveraging their full potential, ensuring that facilities can function smoothly with minimized risks and costs.