Sand casting parts have long been a cornerstone in the manufacturing industry, offering a versatile solution for producing complex metal components. Their continued popularity underscores the technique’s reliability, cost-effectiveness, and adaptability. To produce such parts not only demands intrinsic knowledge of the process but also an understanding of material science and design principles, which aligns with the high standards of Experience, Expertise, Authoritativeness, and Trustworthiness celebrated in modern engineering.
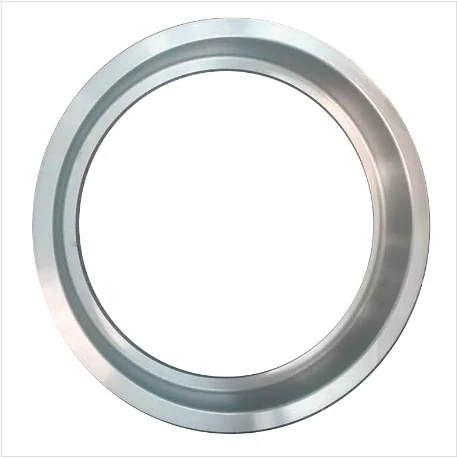
In sand casting, molten metal is poured into a sand mold to create intricate shapes. One of the key advantages of sand casting parts is their ability to accommodate high degrees of design complexity, which can be particularly beneficial when creating intricate geometries that other processes might struggle to replicate. This method allows designers to experiment with dimensions and scale, thus encouraging innovation in product design and development. The freedom found in sand casting expands the horizon for industries such as aerospace, automotive, and mechanical systems, where intricate parts and unique specifications are often required.
A notable experience in the realm of sand casting is the synergy achieved when the right materials meet precise engineering. Foundries often employ a blend of clays, binders, and sands with selected properties that contribute to mold integrity and dimensional accuracy. The ability to tailor the sand mixture to meet specific part requirements speaks to the professional expertise of foundry technicians, whose knowledge ensures that each casting is up to standard. This expertise is rooted in an understanding of both the mechanical properties required by the application and the physical behavior of various metals during the cooling process.
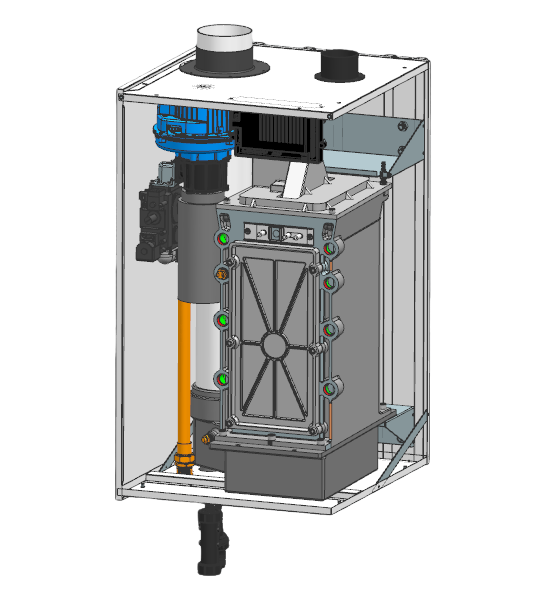
The process of creating sand casting parts is as much an art as it is a science. Successfully manufacturing a high-quality component involves a rigorous method that starts with precise pattern making. Patterns serve as the archetypes for casting molds, requiring skilled craftsmanship and an eye for detail. Mistakes in pattern construction can lead to defects in the final product, which can render a part unusable. Innovations in computer-aided design (CAD) and 3D printing have enhanced pattern making, offering exacting standards of design precision that bolster the authority of sand casting as a modern manufacturing process.
sand casting parts
Trustworthiness in sand casting is evidenced by its enduring legacy and the continued trust industries place in this method. This confidence is further reinforced through stringent quality control measures. Non-destructive testing techniques such as X-ray radiography, ultrasonic testing, and magnetic particle inspection are routinely employed to ensure each casting maintains integrity and adheres to specification requirements. This uncompromising stance on quality cements the credibility of sand casting parts in demanding applications.
Companies investing in sand casting offer clients a unique selling proposition — the ability to deliver bespoke, large-scale components that maximize strength and durability while minimizing weight and material usage. This dedication to efficiency without sacrificing quality serves industries where the balance between robustness and cost is crucial, such as in transportation and infrastructure.
Sand casting parts continue to demonstrate profound expertise and experience. With the backing of centuries of refinement and adaptation, the process speaks volumes of its authoritativeness in the manufacturing field. Each part becomes a testament to precision engineering, robust material science, and innovative thinking. Future technical advancements promise to fine-tune sand casting even further, enhancing its capability to meet the ever-increasing demands of modern industry.
In capturing the ethos of Experience, Expertise, Authoritativeness, and Trustworthiness, sand casting is not just a manufacturing process; it is a beacon of industrial excellence and credibility. This trust in the process and the professionals behind it ensures that sand casting remains an invaluable asset across diverse sectors, crafting components that are as enduring as the sandcasting process itself.