Cooling water exchangers are indispensable components in industries where temperature regulation is crucial. These devices ensure the efficient functioning of systems by dissipating excess heat, thereby maintaining optimal operational conditions. Drawing insights from decades of industrial use, we delve into their functionality, applications, and best practices, providing readers with a comprehensive understanding backed by real-world examples.
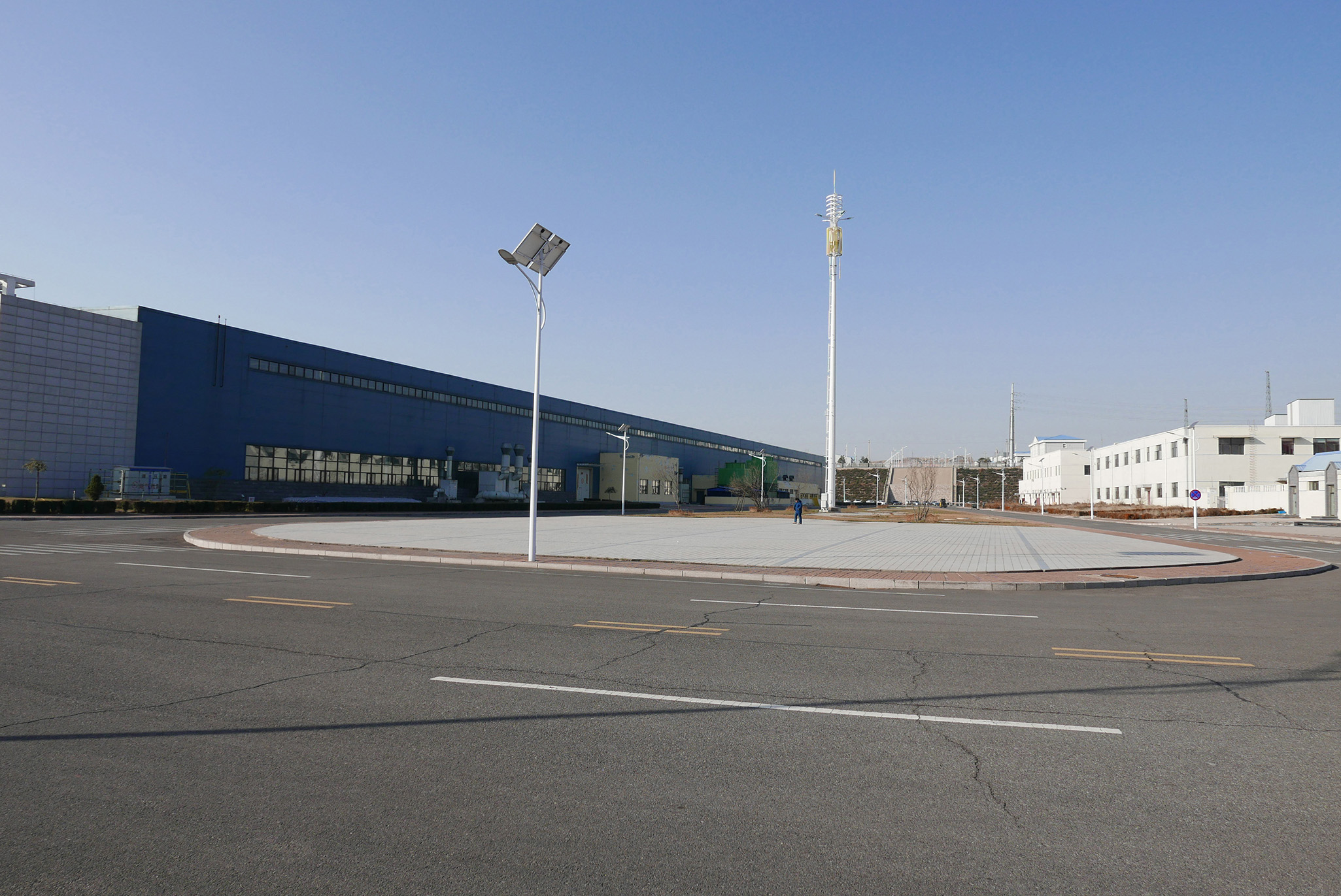
A cooling water exchanger's primary function is to transfer heat from one medium to another, typically from a hot fluid to a cooler fluid, which is often water. This process is vital in numerous industries, including power generation, manufacturing, chemical processing, and even HVAC systems. The performance of these exchangers directly impacts the efficiency and safety of operations.
From an expert perspective, selecting the right cooling water exchanger involves several critical considerations. The material composition is paramount; commonly, exchangers are made from stainless steel, titanium, or copper alloys due to their excellent corrosion resistance and thermal conductivity. For instance, stainless steel is often preferred in the chemical industry for its robustness against corrosive agents.
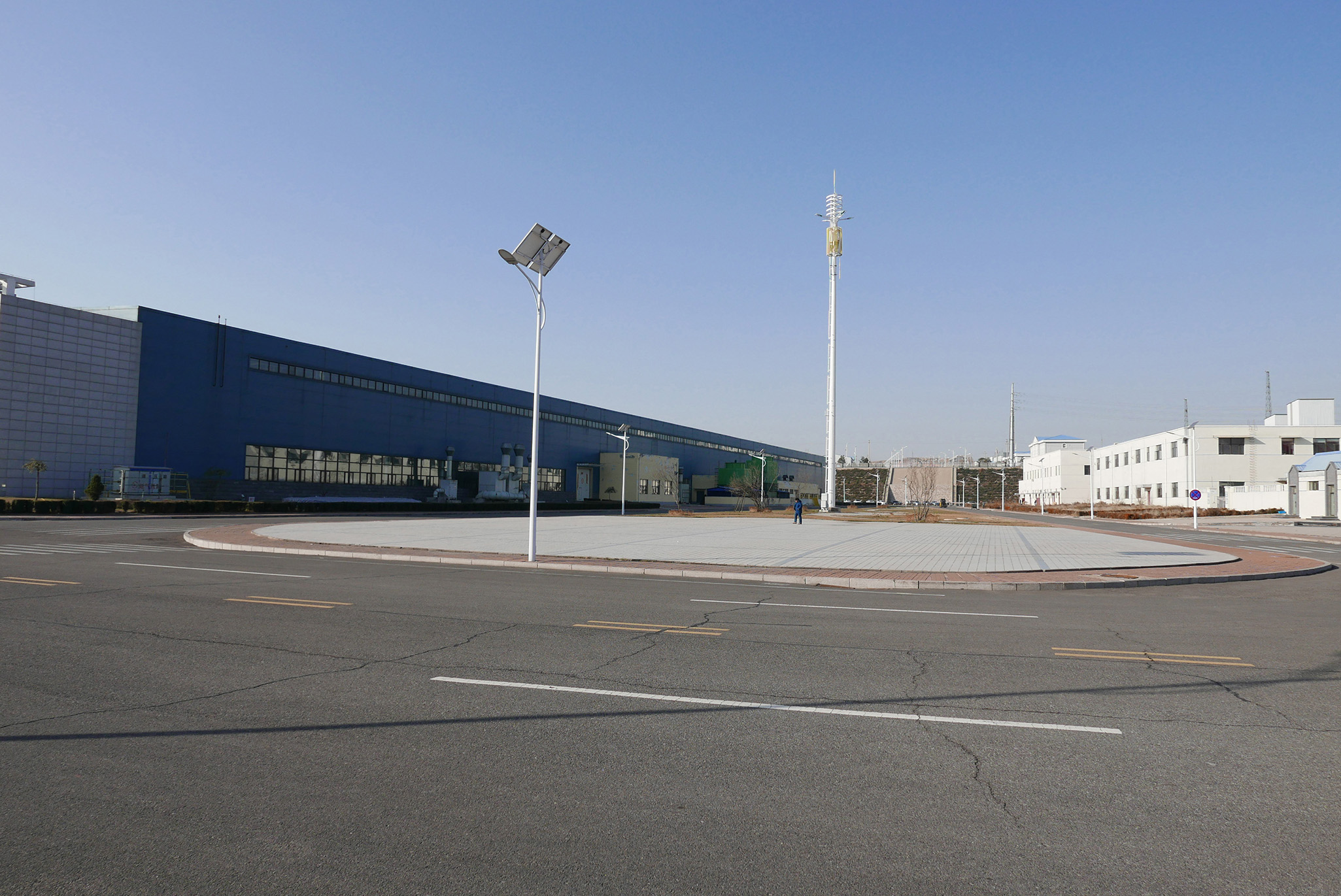
The design configurations, such as shell-and-tube, plate, or air-cooled heat exchangers, each have unique advantages. Shell-and-tube exchangers, known for their durability and ability to handle high-pressure environments, excel in heavy industrial applications. In contrast, plate heat exchangers offer compactness and efficiency, making them suitable for space-constrained installations.
In real-world applications, correctly sizing a cooling water exchanger speaks volumes about efficiency and cost-effectiveness. An oversized exchanger can lead to unnecessary expenditure, while an undersized unit might cause overheating and equipment damage. Using advanced simulation tools, engineers can predict thermal performance, ensuring that the chosen exchanger meets specific operational needs without excess.
Operational experience underscores the significance of maintenance in prolonging the life of cooling water exchangers. Regular cleaning, particularly in environments with hard water, prevents fouling—a common issue that reduces heat transfer efficiency. Employing techniques such as backflushing and chemical cleaning can effectively mitigate scaling and biofouling, ensuring optimized performance.
cooling water exchanger
The authoritative voice in industrial cooling solutions, ASME (American Society of Mechanical Engineers), provides guidelines that underscore the maintenance and safety standards for these exchangers. Adhering to these standards not only ensures the safety and reliability of operations but also maximizes the lifespan of the equipment.
Trust in cooling water exchangers is often established through rigorous testing and certification. Manufacturers typically subject these devices to pressure tests, leak detection, and thermal performance analysis, with documentation providing traceability and reliability assurance. This trust is further bolstered by customer testimonials and case studies demonstrating successful installations and long-term performance.
Among the expert community, the development of eco-friendly and energy-efficient cooling water exchangers is a significant trend, aligning with global sustainability goals. Innovations, such as the incorporation of advanced materials and energy recuperation systems, reduce environmental impact while optimizing operational efficiency.
In considering the future of cooling water exchangers, digitalization and smart technologies hold promise. IoT-enabled exchangers can offer predictive maintenance alerts and performance analytics, minimizing downtime and operational costs. As industries strive for smarter, more integrated systems, the integration of such innovative features into cooling solutions becomes not just advantageous, but essential.
To wrap up this exploration, those in search of a reliable cooling water exchanger must weigh options carefully, considering operational demands, material and design features, and maintenance practices. Partnering with reputable manufacturers and leveraging the latest technological advancements ensures not only effective cooling solutions but also a future-oriented approach toward industrial temperature management needs.