Cast silicon aluminum alloy heat exchangers are the unsung heroes of modern thermal management systems, known for their exceptional thermal conductivity, lightweight properties, and versatility across a range of high-demand applications. Their integration into advanced industrial and consumer solutions underscores not just a trend, but a significant evolution in engineering materials science, promising enhanced performance and sustainability.
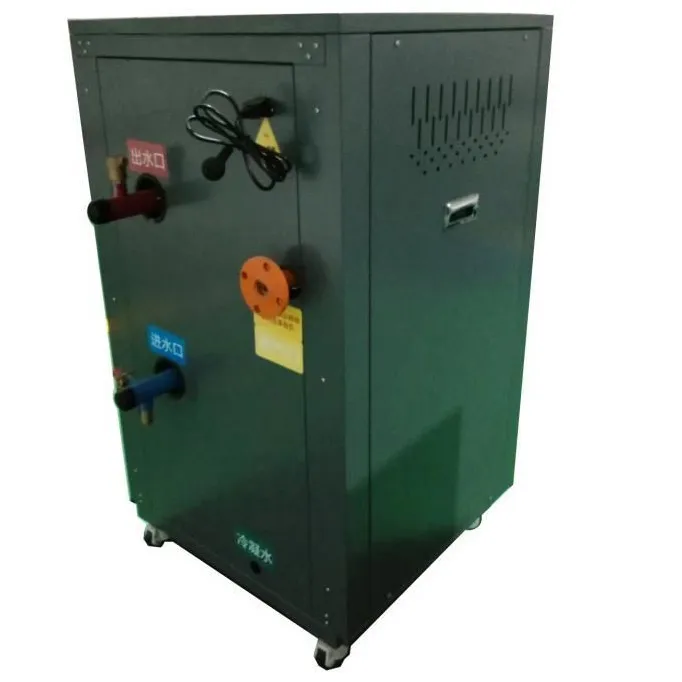
In the realm of thermal management, material choice is critical.
Silicon aluminum alloys, renowned for their synergistic properties, provide an outstanding solution for heat exchangers. This alloy combines the high thermal conductivity of aluminum with the additional structural integrity imparted by silicon, resulting in a material that can withstand high operational temperatures and resist thermal fatigue. These qualities ensure longevity and reliability, which are crucial for applications ranging from automotive systems to aerospace engineering.
One of the key attributes of these heat exchangers is their efficiency. In automotive and HVAC systems, where managing heat is crucial for both performance and safety, silicon aluminum alloys provide a significant advantage. Their ability to rapidly dissipate heat ensures that systems remain within optimal operating temperatures, improving efficiency and reducing the risk of overheating-related failures. This not only enhances performance but also results in energy savings, aligning with the global push towards more sustainable technologies.
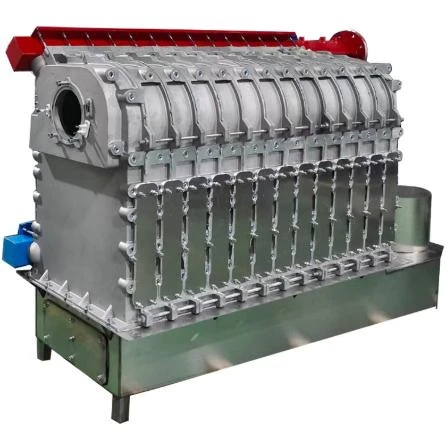
Expertise in the design and manufacturing of cast silicon aluminum alloy heat exchangers is vital. The casting process must be meticulously controlled to achieve the desired microstructure and mechanical properties. Experience in alloy composition and casting techniques ensures minimal defects and maximizes thermal performance. Industry leaders leverage advanced simulation tools and testing protocols to refine their products, ensuring that each unit meets stringent quality standards.
cast silicon aluminum alloy heat exchanger
Moreover, the authority these companies command in the market is reinforced by their commitment to innovation and sustainability. By continuously investing in research and development, manufacturers are able to push the boundaries of what is possible with silicon aluminum alloy technology. Cutting-edge methods like 3D printing and additive manufacturing are being explored to create even more complex and efficient designs, promising a future where heat exchangers are more effective, customizable, and quicker to produce.
Trust in these products is further bolstered by rigorous testing and quality assurance processes. Before reaching the market, each heat exchanger undergoes comprehensive testing to ensure it meets both regulatory standards and customer expectations. This dedication to quality ensures that end users can rely on these components for critical applications, knowing they will perform consistently under demanding conditions.
Educational initiatives also play a crucial role in expanding understanding of the capabilities and benefits of cast silicon aluminum alloy heat exchangers. By providing extensive resources and training for engineers and designers, manufacturers ensure that the full potential of these materials can be leveraged, resulting in better-designed systems that fully utilize the capabilities of silicon aluminum alloys.
In conclusion, cast silicon aluminum alloy heat exchangers are not just components; they are advanced solutions that represent a significant step forward in thermal management technology. Their combination of efficiency, reliability, and sustainability makes them indispensable in various industries, marking a paradigm shift in how we manage heat across a range of applications. As we continue to innovate and explore new frontiers, these heat exchangers will undoubtedly remain at the forefront, driving both technology and efficiency in the quest for better thermal management solutions.