In the world of manufacturing and production, casting stands as one of the most innovative and essential processes. Casting involves pouring liquid materials into a mold to solidify into a specific shape. This time-honored method has evolved dramatically, offering vast potential for innovation and efficiency, particularly in product manufacturing. As a focal point of engineering prowess and industrial acumen, casting holds sway over various sectors, from automotive to aerospace, plumbing to construction.
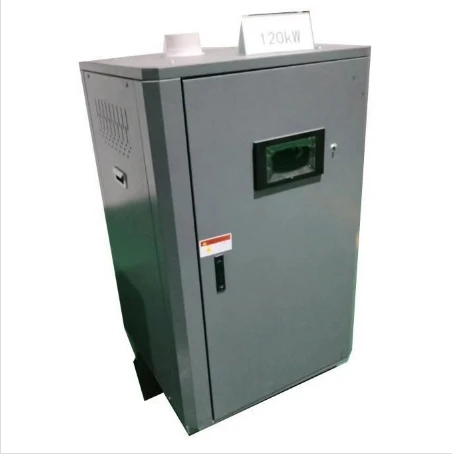
The complexity and versatility of casting have given rise to numerous techniques, each with its unique advantages. Among these, sand casting, die casting, investment casting, and centrifugal casting are the most prevalent. Each offers specific benefits based on the material used, the detail of designs, and production scale. For instance, sand casting, one of the oldest techniques, is highly adaptable to complex geometries and large parts, making it indispensable in heavy machinery industries. Die casting, known for its high-speed production capabilities and superior surface finishes, finds its niche in producing mass quantities of small-to-medium-sized parts.
Emphasizing expertise, casting processes require a profound understanding of materials science. Knowing how different metals react under heat and pressure, for example, is critical for achieving the desired properties in the finished product. Aluminum, copper, and zinc are commonly used metals, each providing unique advantages. Aluminum is lightweight with good corrosion resistance but requires precision to prevent defects. Copper offers excellent thermal and electrical conductivity, crucial in electrical applications, while zinc provides a good balance of strength and ductility for various applications.
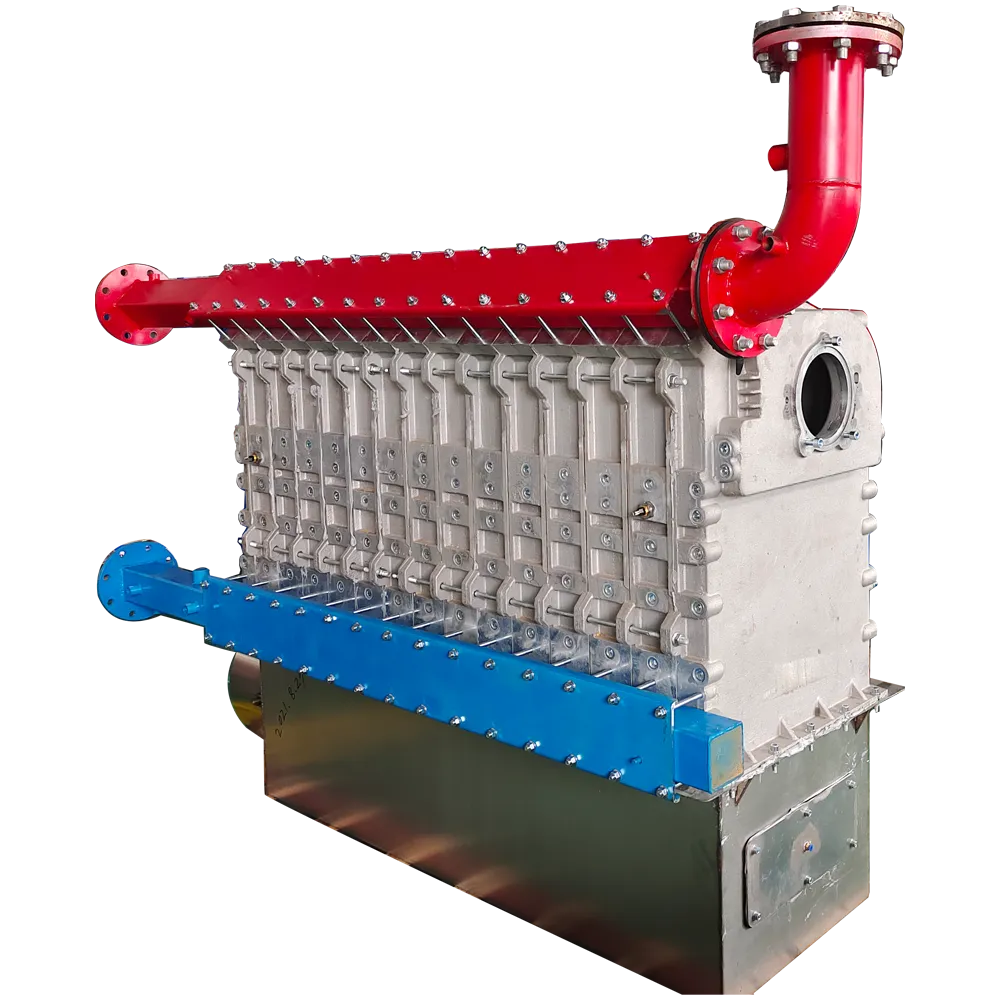
One of the core challenges in casting is avoiding defects, such as porosity, metal penetration, and mold mismatching, which demand technical excellence and cautious process management. Here, experience plays a pivotal role. Manufacturers that excel in casting have honed their processes over years, if not decades. This accumulated know-how ensures a high level of expertise in troubleshooting and process improvement, critical for producing high-quality, reliable products.
Trustworthiness in casting comes from adherence to stringent industry standards. Compliance with ISO regulations,
for instance, is non-negotiable. Companies must maintain comprehensive quality control systems to ensure every casting meets specific dimensions and mechanical properties. Authority in this field is commonly demonstrated by third-party certifications and a proven track record of successful projects in various industry applications.
casting
Moreover, advancements in technology have made significant impacts on casting. The integration of computer-aided design (CAD) and computer-aided manufacturing (CAM) in casting processes has increased accuracy and efficiency. Automated systems help streamline production, reducing waste and minimizing human errors. Furthermore, 3D printing technology has entered the casting arena, particularly in pattern creation, providing unprecedented design flexibility and faster prototyping, transforming concepts into functional parts quicker than traditional methods.
Sustainable practices have also become a vital aspect of modern casting operations. Eco-friendly approaches, like using recycled materials and optimizing energy usage, underscore a commitment to environmental stewardship. Additionally, innovations in mold materials that are recyclable or biodegradable contribute to reducing the ecological footprint of casting activities.
Leading manufacturers in the casting industry not only focus on technological advancement but also on building a skilled workforce capable of driving quality and innovation. Investing in ongoing training and development ensures that staff remain at the cutting edge of casting techniques and technologies. This investment in human capital underscores a company's commitment to expertise and reliability.
When selecting a casting supplier, businesses seek those that exhibit a robust portfolio, documenting successful collaborations across industries. Testimonials from satisfied clients and partnerships with major industrial players serve as powerful endorsements of a supplier’s capabilities and reliability.
In conclusion, the art and science of casting blend to create a dynamic and challenging field with immense potential for innovation. Expertise, quality assurance, and technological integration are cornerstones of excellence in casting. Those who master these elements not only meet the demanding needs of modern production but also set new standards in manufacturing.