Tube in tube heat exchangers are a remarkable solution within the realm of thermal management, offering unparalleled efficiency and reliability for a wide range of industrial applications. Their innovative design and impressive performance metrics make them indispensable in various sectors, from chemical processing to HVAC systems. Drawing on years of expertise and a deep understanding of fluid dynamics and heat transfer principles, these exchangers exemplify excellence in engineering and design, lending themselves to countless applications where reliability and precision are key.
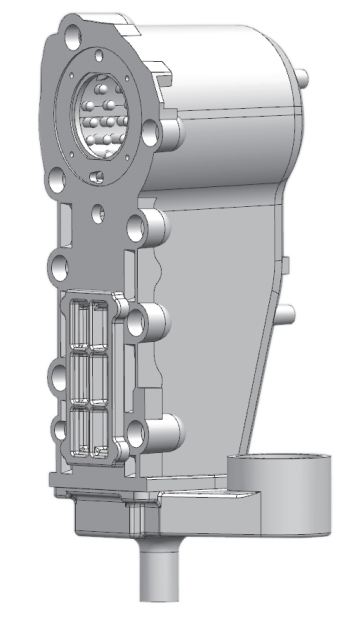
Tube in tube exchangers operate on a simple yet highly effective principle by placing one tube within another and allowing different fluids to flow through each, they facilitate efficient heat transfer between the two fluids without mixing them. This configuration is particularly beneficial for processes requiring strict hygiene and fluid segregation, such as food and beverage production or pharmaceutical manufacturing. The outer tube acts as a protective barrier, shielding the inner tube from external contaminants and ensuring the purity of the media being processed.
For industries focused on maximizing energy efficiency, tube in tube exchangers offer a highly effective solution. Their design minimizes heat loss, ensuring that the thermal energy is directed precisely where it is needed. The counter-flow configuration, where the fluids move in opposite directions, enhances the exchanger’s ability to transfer heat efficiently, resulting in significant energy savings and reduced operational costs. Due to this configuration, these heat exchangers are capable of reaching higher overall heat transfer coefficients compared to other designs.
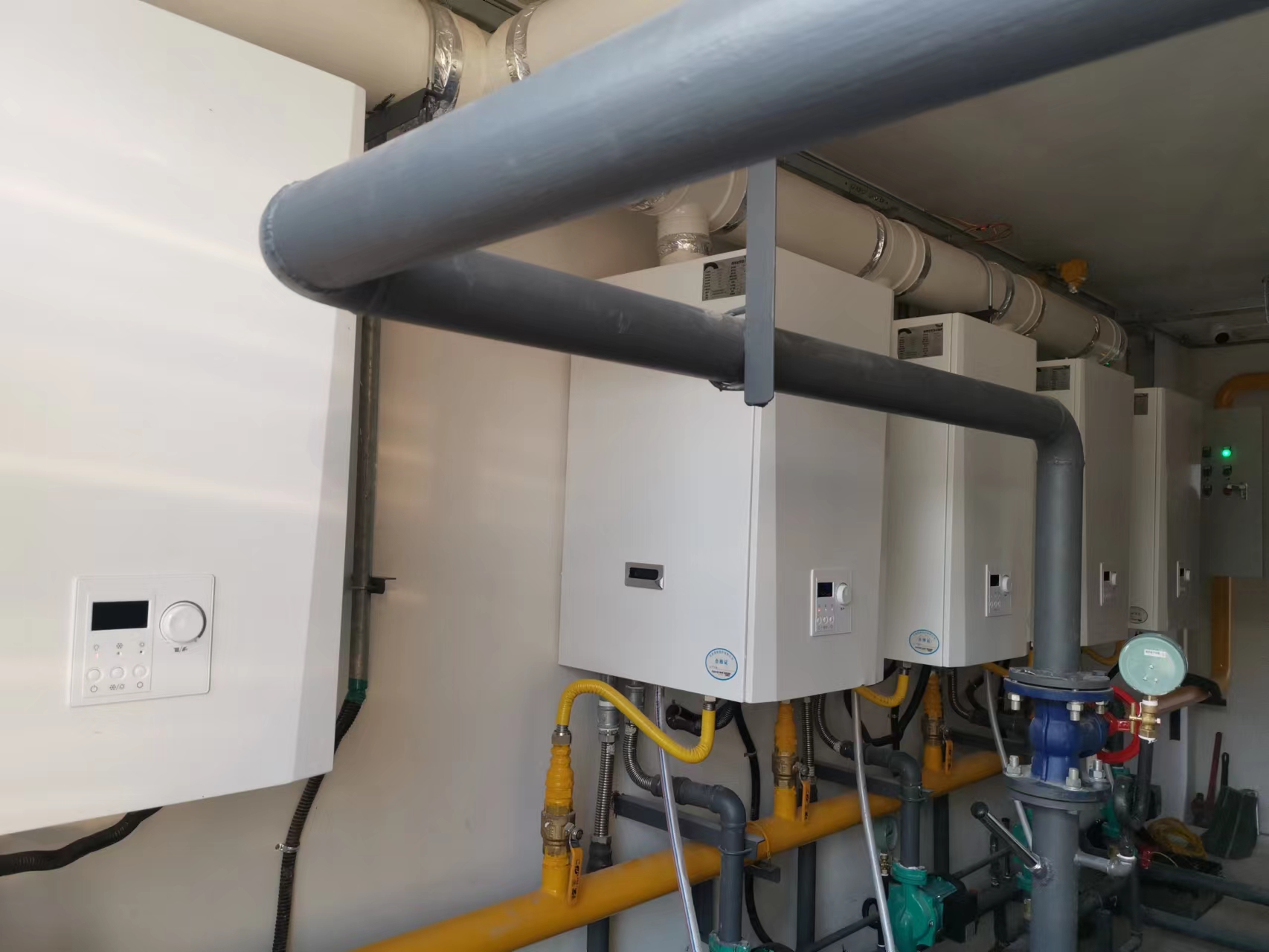
The construction of tube in tube exchangers often involves materials such as stainless steel or other durable alloys, selected for their high thermal conductivity and corrosion resistance. This choice of materials not only extends the lifespan of the exchangers but also enhances their suitability for harsh operating environments. From handling corrosive chemicals in petrochemical plants to dealing with high-pressure steam in power generation facilities, tube in tube exchangers deliver consistent performance and reliability.
From a maintenance perspective,
these exchangers provide outstanding ease of service. The straightforward design allows for quick disassembly, inspection, and cleaning, reducing downtime and maintaining operational efficiency. This is particularly important in industries where service interruptions can lead to significant financial losses. By investing in tube in tube exchangers, companies can significantly improve their system uptime and reliability.
tube in tube exchangers
Furthermore, the capability of these exchangers to handle a wide range of temperatures and pressures makes them versatile solutions for complex thermal management challenges. When designed and implemented correctly, they are ideal for processes that involve extreme temperature differentials or require rapid heat dissipation.
For those in need of bespoke solutions, manufacturers offer customization options for tube in tube heat exchangers, allowing businesses to tailor the exchangers’ features to their specific requirements. These customizations can include adjustments in tube diameters, materials, and the incorporation of additional features such as heat recovery systems for enhanced efficiency.
In comparison to other types of heat exchangers, such as plate or shell-and-tube models, tube in tube systems provide distinct advantages in terms of space efficiency and installation flexibility. Their compact footprint allows them to be installed in confined spaces where traditional exchangers may not fit, providing a crucial advantage in facilities where maximizing floor space is a priority.
Beyond their practical advantages, investing in tube in tube exchangers also demonstrates a commitment to sustainable practices. Their energy-efficient design contributes to reducing overall carbon footprints, aligning with contemporary environmental standards and helping companies to meet regulatory compliance more easily.
In summary, tube in tube exchangers offer an exemplary balance of efficiency, durability, and adaptability. Their ability to handle demanding conditions, coupled with their ease of maintenance and significant energy savings, underscores their status as essential components in modern industrial processes. For businesses aiming to optimize their heating and cooling operations while ensuring reliable, long-term performance, tube in tube heat exchangers represent a wise choice.