Crafting a heat exchanger involves blending an intricate knowledge of thermodynamics with cutting-edge engineering practices. As a critical component in various industrial applications, a well-designed heat exchanger can significantly impact energy efficiency and process optimization. Here, we delve into the nuanced steps of designing a heat exchanger that not only meets operational demands but also excels in performance and durability.
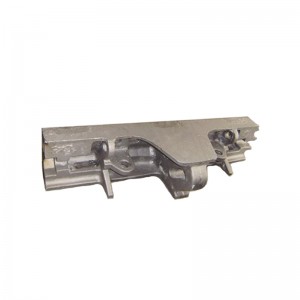
Understanding the Core Functions
At the heart of any heat exchanger design is a thorough understanding of its primary function to efficiently transfer heat between two or more fluids—namely liquids, vapors, or gases—without allowing them to mix. This principle dictates the choice of materials, design configuration, and operational parameters. It's essential that the designer comprehends the thermal properties of the media involved, as well as the temperature and pressure ranges the device will endure.
Selecting the Appropriate Type
Heat exchangers come in various types, including shell and tube, plate, air-cooled, and more. Each design offers distinct advantages suited to specific applications. For instance, shell and tube heat exchangers are renowned for their versatility and ability to handle high pressures and temperatures, making them ideal for industries such as petrochemical processing. In contrast, plate heat exchangers, with their compact structure, offer high efficiency and are often used in food processing and HVAC systems. An expert's insight into the operational environment is crucial to selecting an appropriate type that maximizes performance and reliability.
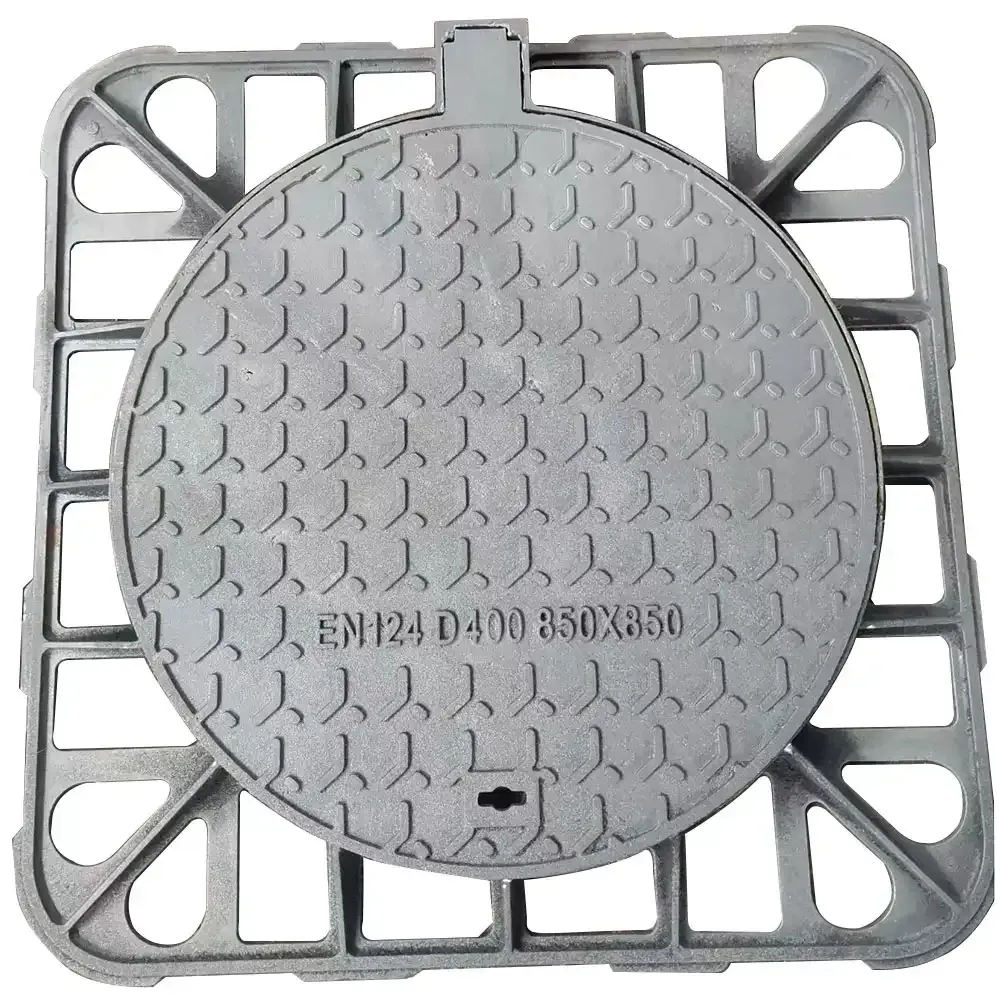
Material Considerations
Choosing the right materials is pivotal in heat exchanger design. Factors such as thermal conductivity, corrosion resistance, and mechanical strength guide this decision. Engineers often opt for metals like stainless steel, titanium, and copper alloys, given their excellent heat conduction and robust corrosion resistance. The compatibility of these materials with the fluids in question and the operating conditions further influences this choice. Expert knowledge in material science ensures that the selected materials enhance the durability and life span of the equipment.
Designing for Efficiency
Efficiency is the cornerstone of any successful heat exchanger. Experts employ advanced thermodynamic calculations and simulations to optimize the surface area for heat transfer, fluid flow paths, and pressure drops. Techniques such as computational fluid dynamics (CFD) modeling allow for precise predictions of heat transfer coefficients and flow patterns, leading to a refined design that minimizes energy consumption and maximizes throughput. This level of expertise ensures that the product not only meets but exceeds industry standards for performance.
making a heat exchanger
Incorporating Technological Innovations
Recent advancements in technology have introduced innovations that enhance the functionality of heat exchangers. Incorporating smart sensors and IoT technologies can provide real-time monitoring and predictive maintenance capabilities, ensuring the exchanger operates at peak efficiency throughout its service life. Automated control systems adjust operational parameters dynamically, improving efficiency and reducing wear. Implementing these technologies requires expertise in both hardware integration and software development, highlighting the intersection of traditional engineering and modern technological evolution.
Ensuring Regulatory Compliance and Safety
Designing a heat exchanger also necessitates a rigorous adherence to industry standards and regulations. These standards, set forth by organizations like ASME and API, ensure safety, reliability, and environmental sustainability. Professionals in the field stay abreast of evolving regulations and incorporate them into the design process, guaranteeing compliance and instilling user confidence. Furthermore, conducting comprehensive testing and validation helps in identifying potential safety hazards, thus reinforcing the product's trustworthiness.
Sustainability and Environmental Impact
In today’s environmentally-conscious climate, sustainability is a critical consideration in the design of heat exchangers. Implementing eco-friendly practices and selecting recyclable materials can reduce the environmental footprint. Designing for minimal energy consumption not only aligns with global sustainability goals but also offers cost savings for the end user. Engineers with an eye toward sustainable design make decisions that benefit both the planet and the bottom line.
In summary, the journey of making a heat exchanger marries extensive expertise with innovative engineering practices. Through thoughtful design, material selection, technological integration, and compliance with regulatory standards, heat exchangers are tailored to offer exceptional performance and reliability. This amalgamation of proficiency and authority ensures that the final product stands unmatched in the ever-evolving industrial landscape.